The client from Chemical Industry and Effivity PRO have entered a collaboration and set a new standard in the chemical industry for Quality Management Systems (QMS) and Health, Safety, and Environmental (HSE) compliance. The partnership will leverage Effivity's innovative software solutions to enhance global manufacturing and operational standards. By doing so, the goal is to achieve compliance across all levels of operation and create an organisation that is ready and prepared for the future in the face of evolving markets.
About Our Client
Our Client from Chemical Industry is a globally recognised leader in the field of acrylic-based products. They have a rich heritage of innovation and excellence. With a network of 22 plants and 14 manufacturing sites spread across continents, our client plays a central role in shaping the future of the acrylic industry.
Our client is committed to sustainability and innovation, continually seeking ways to improve its products and processes. The integration of QMS and HSE software is a strategic move to uphold the highest standards of quality and safety, reduce environmental impact, and enhance customer satisfaction through operational excellence.
About Effivity PRO
Effivity is an industry leader in innovative software solutions designed to streamline QMS, HSE, and other compliance requirements. It is known for its comprehensive suite of modules that cater to various ISO standards.
Effivity simplifies compliance management and makes it accessible and manageable for organisations of all sizes. Effivity's software platforms are customisable, scalable and user-friendly. With Effivity, we ensure that organisation's can focus on the strategic aspect of the business leaving compliance management processes to us.
Solutions Offered to our Client
As a global innovation leader, an unprecedented collaboration unfolds, encompassing 22 plants and 14 manufacturing sites worldwide. Aside from the basic suite of modules that comes with Effivity's QMS and HSE management software, we offered a few customised solutions specific to our client's operational requirements. Some of these solutions include:
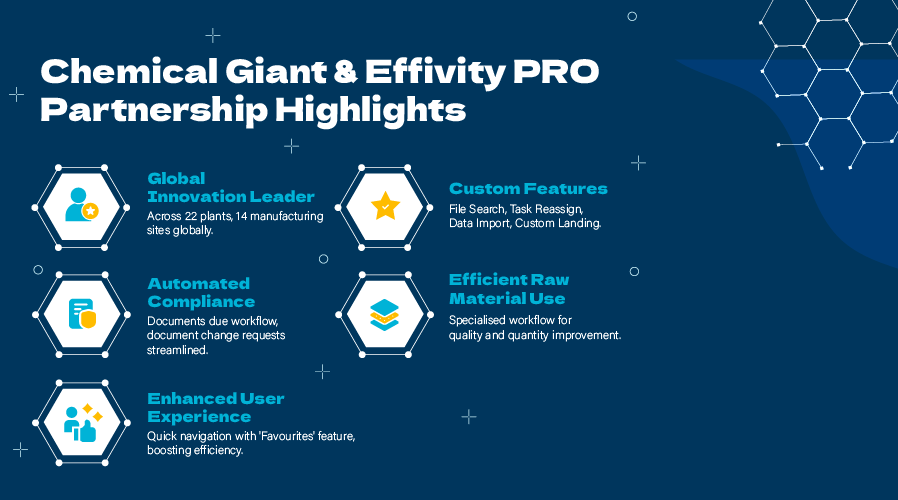
File Search
Our client expressed a need for a more intuitive search functionality within their Documented Information Module. They wanted the ability to probe the full text of documents and not just metadata.
Effivity responded by integrating an advanced 'File Search' feature, which employs a comprehensive search engine to scrutinise every word within documents. With this, we were able to align search results with user queries more accurately. From a QMS and HSE perspective, this enhances the efficiency and responsiveness of compliance and documentation management.
Reassign Task
Effivity introduced a 'Reassign Task' function to address potential workflow disruptions caused by employee absence due to leave, vacation, or resignation. This feature allows for the swift reassignment of tasks to ensure continuity and prevent bottlenecks. As a result, the organisation was able to achieve a seamless transfer of responsibilities.
This type of flexibility is crucial to maintain operational efficiency and flow, which also helps maintain compliance without interruptions.
Data Import
Effivity tailored a 'Data Import' feature to their client keeping in mind the challenges associated with migrating existing data into a new system. This solution was designed to efficiently integrate a large volume and variety of data. As a result, we were able to reduce setup time and facilitate a smoother transition to the new QHSE system. This feature also reduced downtime in the operations.
Landing Page
The team highlighted the need for a more relevant initial view upon system login. As a response, we developed a customisable 'Landing Page' feature. Here, the user can configure their landing screen and add elements of their choice. This makes the software more adaptable to individual user preferences and workflows.
Favourites
Effivity created a 'Favourites' feature to enhance navigation and user experience within the software platform. This innovation allows users to bookmark frequently accessed screens or records. As a result, it reduces the time taken to navigate the system and retrieve information or add inputs.
Documents "Due" Workflow
Effivity introduced an automated 'Documents Due' workflow to prevent documents from becoming outdated and ensure timely revisions. This system automates reminders for document revisions based on a preset "Revision Date". It effectively reduces the risk of non-compliance incidents.
Document Change Request
The 'Document Change Request' (DCR) feature was created to foster continual improvement to changing market dynamics. This allows for the controlled functioning of the change management software while ensuring that all new processes are implemented and sustained. DCR helped them to keep pace with market and regulatory changes and maintain QMS compliance.
Raw Material Workflow
Effivity designed a specialised 'Raw Material Workflow' to address client’s specific needs for managing raw material availability and quality. This workflow ensures the efficient use of raw materials, directly impacting the quality and quantity of output.
Why Effivity is the Top Choice?
Just like Our Chemical Client, Effivity's quality management software is a top choice for leaders across industries. Here are some reasons why Effivity's software solutions stand in the market:
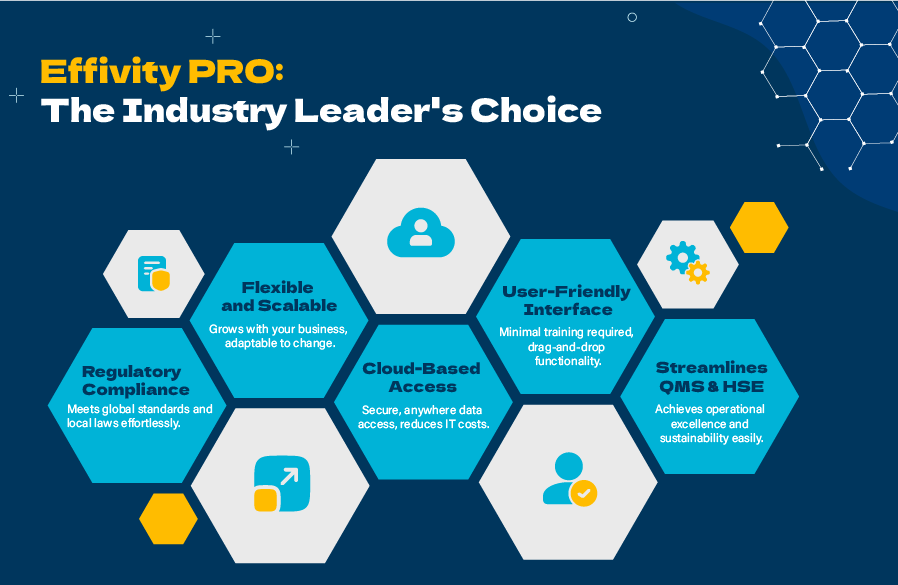
1. Compliance Management
The Effivity Health and Safety management software is designed with compliance in mind. It takes into account all standards, regulations, and legal requirements at the local and international levels to help your organisation stay on top of your compliance management strategies.
2. Scalable and Adaptable
Effivity's scalable and adaptable software differentiates it from other digital solutions. We understand that businesses evolve and require systems that can grow in tandem and adapt to changing industry demands.
With Effivity, you can effortlessly add or remove modules, modify existing ones, and ensure that your operations are future ready. This flexibility empowers Companies from Chemical industry to stay agile and respond quickly to new opportunities.
3. Cloud-Based Accessible Solution
The cloud-based accessible solution that Effivity provides is a significant shift from traditional, hardware-intensive setups. With no need for expensive IT infrastructure, you can store data securely on the cloud.
With cloud computing and storage, data can be accessed anywhere and anytime. This level of accessibility with advanced safety features allows information to be available when needed while also protecting sensitive data from unauthorised access.
4. User-Friendly Interface
Effivity's user-friendly interface is designed with a drag-and-drop interface. The intuitive platform eliminates the steep learning curve associated with complex software. This means employees can easily navigate through the system and make it part of their daily routine.
The integration into daily operations ensures that the transition to using efficiency for better compliance is smooth. It also cuts down on the costs for employees, specialised staff, and extensive training. This makes it a cost-effective solution for all businesses.
5. Streamlines QMS & HSE
Effivity's cutting-edge platform simplifies Quality Management System (QMS) and Health, Safety, and Environment (HSE) processes, empowering businesses to effortlessly achieve operational excellence and sustainability goals.
By seamlessly integrating into daily operations, Effivity reduces the need for extensive training and specialized personnel, offering a cost-effective solution for businesses of all sizes. Experience the ease of enhancing operational performance and sustainability with Effivity.
Final Thoughts
A Giant player in Chemical's Industry successful partnership with Effivity PRO is an example of how organizations can implement QMS and HSE software to enhance compliance and improve efficiency. Effivity is the software of choice for many leading corporations that aim to enhance their performance, efficiency and sustainability while maintaining continuous compliance with standards and regulations.
You can try Effivity's Quality Management Software to automate quality control processes in your organisation. Contact our team for a free consultation and trial today!