However, simply treating the symptoms of a problem often leads to recurring issues. The key is to understand why these issues are happening in the first place, and that's where root cause analysis comes in.
This approach helps businesses delve deeper to identify the fundamental causes of a specific problem, paving the way for more lasting and effective solutions.
Let’s understand what root cause analysis is and how you can conduct an effective root cause analysis for your business.
What is Root Cause Analysis?
Root cause analysis (RCA) refers to the method of identifying and understanding the underlying cause of a problem and looking for specific solutions that directly address that problem. This way, you can solve the real cause of an issue rather than just treating temporary symptoms.
For instance, if a machine in a factory keeps breaking down, simply repairing it each time is treating the symptom. An RCA might reveal that the underlying cause is inadequate lubrication due to a faulty oil pump. By replacing the oil pump (the root cause), the recurring breakdowns are prevented, offering a long-term solution instead of repeated temporary fixes.
Different Techniques of Root Cause Analysis
When you do a root cause analysis, you basically seek answers to the following questions: what exactly happened? How did it happen? Why did it happen? And what actions can prevent it from happening again? Let’s understand the different ways in which you can perform an RCA for your organization.
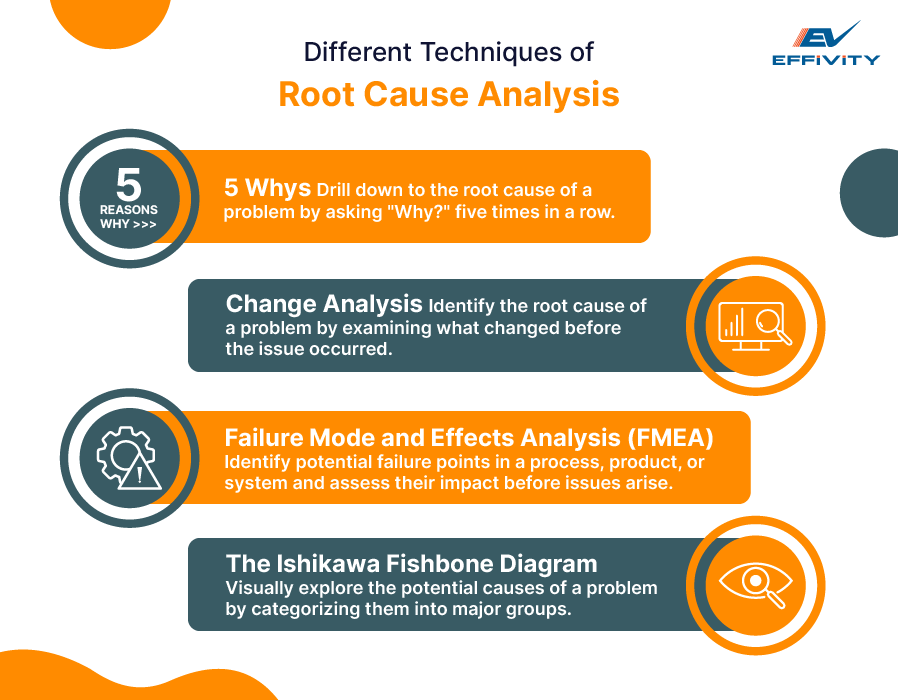
1. The 5 Whys
This is one of the most common and easiest problem-solving strategies. All you need to do is start with a problem statement and then ask “Why?” with each “Why?” driving you closer to the root cause. It goes something like this:
Problem statement: A machine in a factory has stopped working. Why?
The motor overheated and shut down. Why?
The cooling fan on the motor was not spinning. Why?
The fan belt was broken. Why?
It was old and had not been replaced in accordance with the maintenance schedule. Why?
The maintenance schedule was not consistently followed. And with this answer, we finally arrive at the root cause of the problem which is lack of responsibility in following the maintenance schedule.
2. Change Analysis
This root cause analysis technique examines how conditions associated with a particular incident have changed over time. Under this technique, you identify which deviation from the regular process has led to the occurrence of an unfavorable event. This allows you to come up with relevant risk management strategies to solve a business problem.
Risk management software also plays a considerable role in coming up with these strategies. For example, Effivity’s risk management module outlines all the actions required to mitigate risks and regularly monitors the risk environment to ensure that new and emerging risks are identified and assessed promptly.
3. Failure Mode and Effects Analysis (FMEA)
This is a proactive root cause analysis approach that involves predicting potential breakdowns or failure modes in a business product, process, or service and analyzing their impacts on a severity basis. It helps in rectifying issues before they can turn into failures. This approach is applied to establish a cause-and-effect relationship that aims to assess why specific issues occur.
4. The Ishikawa Fishbone Diagram
Another popular RCA technique is creating a fishbone diagram, also referred to as Ishikawa diagram to visually map the cause and effect of an incident. You can think of it as a more visual version of the 5 Whys.
Usually, the process begins by placing the main problem at the center of the diagram, this forms the spine of the fish skeleton. From there, you brainstorm broad categories of potential causes, which branch off like ribs. These ribs are then further broken down into more specific contributing factors, creating a visual map of everything that could be feeding into the issue.
What are the Steps to Conduct an Effective Root Cause Analysis to Solve Business?
The objective of an RCA is simple: uncover the cause of a problem or failure, address it, and prevent any future occurrences. The steps below provide a structured approach to performing a root cause analysis to solve business problems.
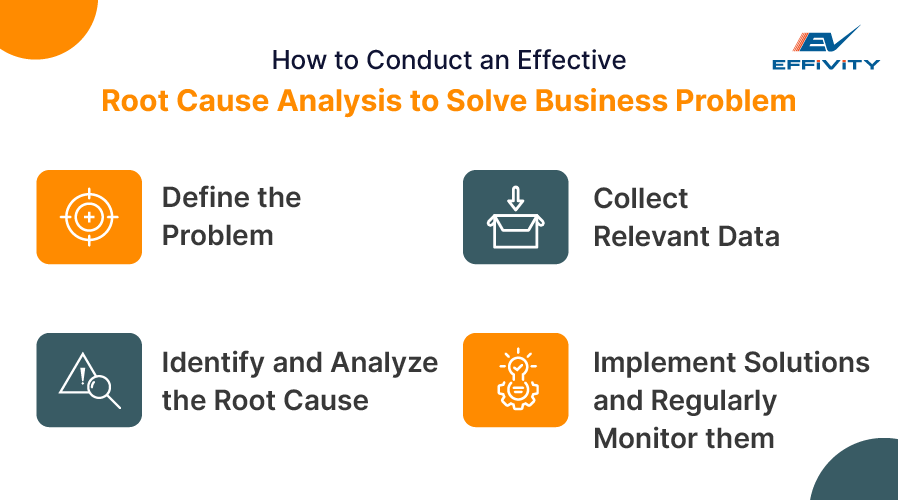
1. Define the problem
The first step is to create a problem statement in a concise way and identify the symptoms associated with that problem. It involves the identification of performance and opportunity gaps within your organization. While the former illustrates the gaps between your organization's intended performance and actual outcomes, the latter reflects something new or innovative your organization can do to create value.
2. Collect relevant data
Next, gather all available documentation and insights related to the issue, such as recorded findings, intervention steps already taken, team involvement, and any additional supporting evidence that could help in thoroughly investigating and pinpointing the root cause for an effective incident management.
3. Identify and analyze the root cause
After the collection of data, you should identify the root cause using one of the techniques and conduct a thorough analysis of each potential root cause, eliminating those that appear less plausible and delving deeper into the ones most likely to have played a role in the incident.
Once the most probable root causes have been determined, their validity should be tested, wherever possible, by simulating the conditions under which the issue might’ve occurred, to confirm their role in triggering the problem.
4. Implement solutions
Once you have identified the root cause, preventive solutions to ensure that the problem won’t happen again. You must carefully outline a comprehensive timeline and corrective action plan on how you can implement the solution including the potential effects on individuals or operating environments.
Additionally, you should also consider factors such as budget, potential roadblocks in implementation, and specific roles of individuals involved in the plan.
After the implementation, another significant step is to carefully monitor and evaluate the performance of the plan to ensure it has effectively addressed the underlying cause.
To successfully implement a corrective action plan, you can use Effivity which provides a comprehensive solution to tackle any problem, whether it’s to maintain compliance with standards like ISO 9001 or improve the overall quality management of your organization.
Summing Up
Root cause analysis is an essential problem-solving method used to pinpoint the exact problem affecting the operational efficiency and quality management of your business.
By employing different root cause analysis techniques, such as the five whys, fishbone diagram, FMEA, and change analysis, you can address what's truly causing an issue, gain the power to fix it permanently and steer your business toward sustainable success.