Implementing the OHSAS 18001 standard for occupational health and safety management systems (OHSMS) is essential for organizations that aim to ensure workplace safety and compliance.
It offers a comprehensive framework to helps organizations manage and mitigate risks associated with health and safety, leading to improved employee well-being and operational efficiency. Adopting OHSAS 18001 involves a strategic approach that makes safety processes a focus of all aspects of business operations, thereby fostering a culture of continuous improvement and proactive risk management.
However, gaining OHSAS 18001 certification can be overwhelming, given the extensive requirements under this standard. To simplify the process, here are the 12 steps that provide information about the elements essential to the OHSAS system.
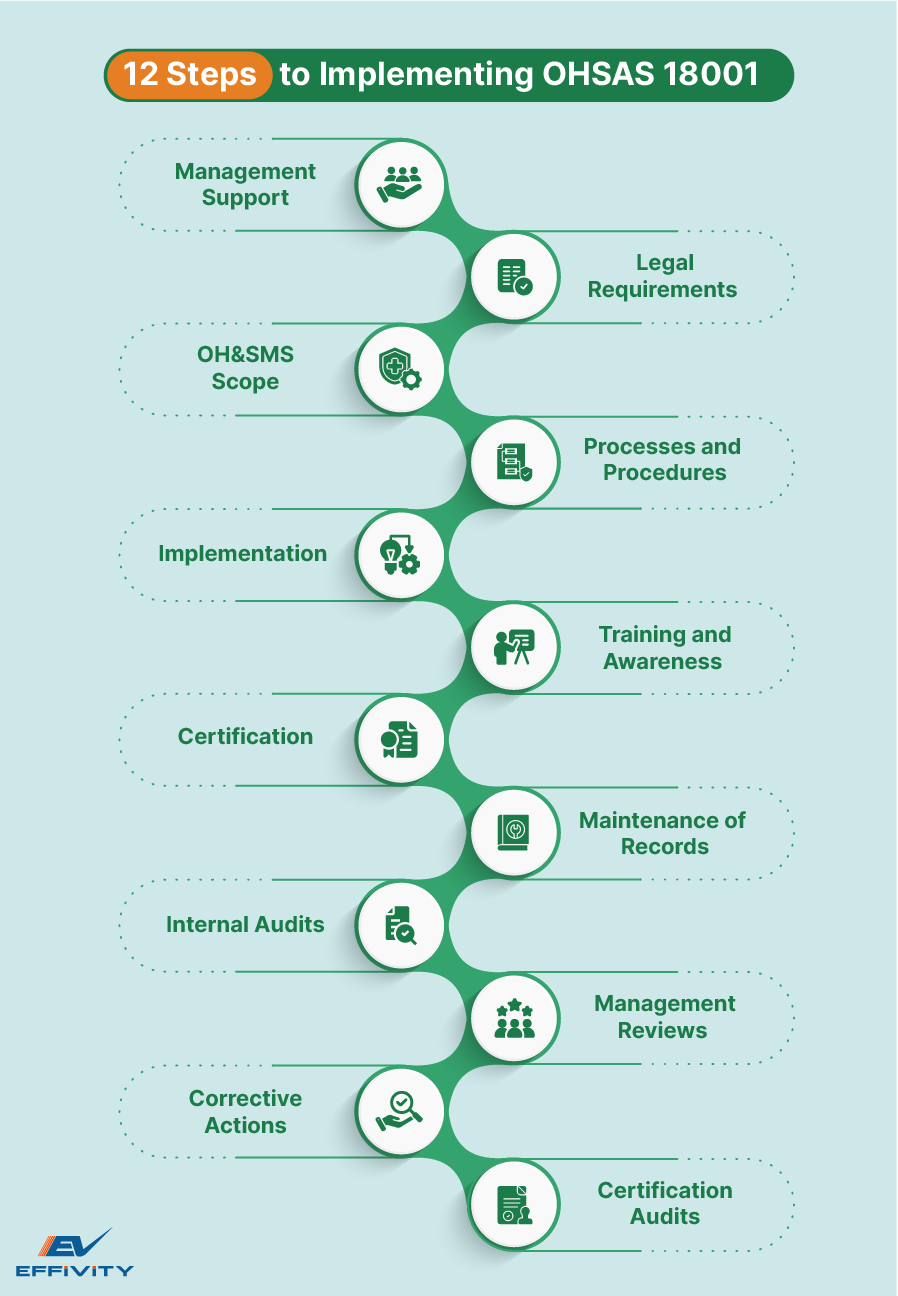
1. Management Support
Getting support from the top management is crucial for effective implementation of the occupational health and safety management system. Management must understand the benefits of an effective OHSMS and provide the necessary resources, including time, personnel, and budget. For this, you must communicate the positive impact on employee safety, legal compliance, and potential financial benefits of OHSAS and decide whether to talk to them individually or conduct a meeting.
2. Legal Requirements
For your health and safety management system to be effective, you first need to know which legal requirements govern the OHSAS 18001 within your industry. For this, check out the regional, national, and international legislation.
Section 4.3.2 of OHSAS 18001 requires the organizations to define the procedures to identify and access the applicable OHS requirements. These requirements must be considered while establishing the OHSMS and must be regularly updated and communicated with the relevant parties.
This step requires you to be updated with the compliance requirements and integrate them with the Occupational Health and Safety Management System.
3. OH&SMS Scope
Depending on your organization and business needs, you might want to implement OHSMS across the entire organization or only a few locations where your business operates.
In this regard, defining the scope of your Occupational Health and Safety Management System involves determining which parts of the organization the system will cover. This decision should be based on the nature of your operations, the associated risks, and the organizational structure. Afterwards, the scope must be clearly documented and communicated to all stakeholders, as it will serve as the foundation for developing your OH&S policy, objectives, and targets.
4. Processes and Procedures
A key aspect of managing occupational health and safety risks within your organization is to define procedures and processes that are consistent across the organization. This includes developing comprehensive policies to
- Identify hazards and risks
- Assess risks
- Define operational controls
- Evaluate emergency preparedness
- Identify the documentation and control needs
Each process should be aligned with the overall objectives of your OHSMS and designed to mitigate identified risks. Also, having detailed documentation will ensure consistency and provide a reference for training and auditing purposes.
5. Implementation
Once you have defined and communicated the key policies and procedures, the next step is to implement them. This involves establishing a hierarchy of controls to manage identified risks, assigning clear responsibilities, and ensuring that all employees are engaged and informed about their roles in the OH&SMS. Effective implementation requires ongoing communication and collaboration across all levels of organization to foster a culture of safety.
6. Training and Awareness
An effective OHSMS is essential to improve the safety procedures within your organization, but are your employees aware of the benefits? Successful OHSMS implementation can only be achieved by educating employees about the need for implementation and their specific roles.
As a result, it becomes important to conduct training sessions that cover the principles of the OHSAS 18001 standard, specific procedures, and individual responsibilities. Start by establishing the process for training sessions – will they be conducted during department meetings or by individual managers?
Continuous training is necessary, especially when you make any changes to processes, procedures, or personnel so that everyone knows how they relate to the OHSMS and their responsibilities.
7. Certification
Next, you must choose the right certification body to get OHSAS 18001 certification once the system has been designed and implemented. Select a certification body and auditors with relevant expertise in your industry, and evaluate their credentials, experience, and feedback from other companies they have worked with.
This chosen body will conduct an external audit of your OHSMS and will grant certification upon successful compliance. A reputable certification body will add credibility to your OHSMS and provide valuable insights during the audit process.
8. Maintenance of Records
Regular record-keeping and maintenance are essential for demonstrating the effectiveness of your OHSMS. You must keep detailed documents of all activities, including risk assessments, training sessions, incident reports, and internal audits. Furthermore, regularly review these records to identify areas for improvement, manage employee responsibilities, and ensure that all processes are functioning as intended.
9. Internal Audits
An internal audit is a vital tool to measure the accuracy and effectiveness of your OHSMS procedures and ensure compliance with OHSAS 18001 requirements. Conducting regular internal audits to identify non-conformances and areas for improvement will provide an opportunity to address issues before the external certification audit.
10. Management Reviews
Management plays a critical role in the successful working and certification of OHSAS 18001 with regular reviews. Regular reviews allow them to determine if the OHSMS is functioning as required. Comprehensive management reviews provide an opportunity to assess the overall health of the system, identify improvements, and ensure adequate availability of resources to meet OHSAS goals and regulatory requirements.
11. Corrective Actions
Any problem identified during internal audits or management reviews must be immediately addressed. This involves identifying and removing the root cause of issues and employing the right corrective actions to address them.
On top of that, corrective actions should be documented, reviewed, and monitored for effectiveness. A proactive approach to corrective actions demonstrates a commitment to continuous improvement and enhances the credibility of your occupational health and safety management system.
12. Certification Audits
The final step involves an external certification audit conducted by the chosen certification body. The auditors will compare your OHSAS processes, plans, and procedures with the OHSAS 18001 standard requirements to identify gaps.
If the auditor identifies gaps, they must be addressed immediately and recorded to demonstrate action. Afterwards, the external auditors can conduct another audit to compare records to plans to see how the non-conformances within your internal audits and process data were addressed.
The auditors will issue an audit report upon completion of the audit, which can also include any corrective actions required. Upon completing the audit, the certification body will recommend your organization for certification, formally recognizing your commitment to occupational health and safety.
In the End
Implementing OHSAS 18001 systematically ensures a safer workplace and compliance with regulatory requirements. With strong management support, comprehensive training, and a commitment to continuous improvement, organizations can effectively manage occupational health and safety risks. Following these 12 steps offers a framework for achieving OHSAS 18001 certification, contributing to the overall well-being of employees and the organisation's success.