If you want to implement an ISO 9001-based quality management software in your business processes, it can be overwhelming to begin with. ISO 9001 standard helps organisations improve their quality processes based on the seven quality management principles.
It aims to allow companies to be more efficient, improve processes and reduce costs to offer products and services that consistently meet customer expectations. As a result, irrespective of the size and nature of your business, 9001 accreditation brings immense benefits to the business by developing a culture of quality and continued improvement.
However, the certification journey can be complex and challenging without proper planning and execution. Here, we're discussing the 10 steps to implement ISO 9001 and get certification to help you manage the process effectively.
Steps to Get ISO 9001 Certification
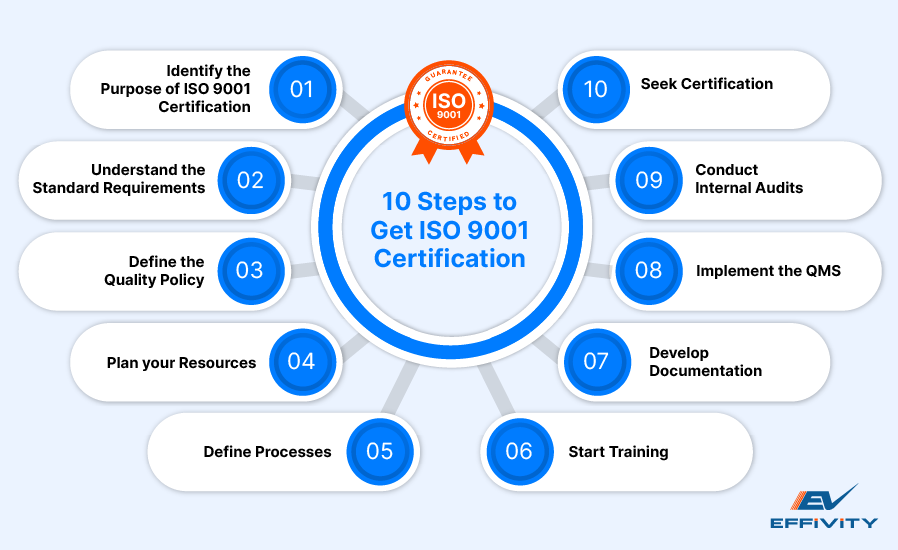
1. Identify the Purpose of ISO 9001 Certification
Why do you want to get ISO 9001 accredited? Perhaps the management thinks it's a good idea because every business is accredited, or your customers demand it. However, unless you understand the benefits of implementation, it might not be as successful for your business.
So, an effective ISO 9001 implementation requires constant support from the top management, who must clearly understand how it can benefit the business and what goals they aim to achieve. In fact, the ISO 9001:2015 version requires that the top management must demonstrate its commitment to quality to all interested parties.
That is why the top management must be aware of the performance of key quality processes, the need for continual improvement and specific customer requirements to start QMS implementation the right way.
2. Understand the Standard Requirements
To effectively implement ISO 9001:2015 , it's crucial to have a deep understanding of its requirements. This involves studying the standard itself, its principles and its clauses.
The standard emphasizes various aspects of quality management, such as leadership commitment, customer focus, engagement of people, process approach and continual improvement. Familiarizing yourself with these concepts lays the groundwork for successful implementation.
Since the ISO standard is universal to all industries, looking for guidelines for a specific sector is not required. Moreover, if your country has a standards authority, there might be a specific version with some changes to cater to the country's legislation.
However, if your business operates internationally in more than two countries, one country's standard might not be accepted in another country. In such a case, you must select the right certification body and understand the requirements thoroughly.
3. Define the Quality Policy
The next step is for the top management to define and outline the Quality Policy and Objectives per ISO 9001 standard in a formal document. The idea is to interpret the various ISO 9001 requirements in the context of your company and make them measurable to allow you to demonstrate continuous improvement.
4. Plan Your Resources
Along with a quality policy, establish an implementation plan that will outline the steps, timelines, responsibilities and resources needed to achieve ISO 9001 certification. Although a formal QMS implementation plan is not required per ISO 9001 regulations, having one can help the organisation better manage and measure its progress.
This plan should be comprehensive and realistic, considering organisational structure, available budget and operational constraints.
5. Define Processes
One of the critical requirements of the ISO 9001 standard is to follow a process-based approach. To achieve this, it is important to define the key quality processes of your business and describe how they interact within the company. A process map tailored to your company's objective is a useful tool.
You must identify the controls, resources, records and documentation required for each process to meet the ISO 9001 requirements. Additionally, validate the process map across the organisation to ensure no interactions are missed. This process map should be reviewed and updated during each stage of implementation before including in the quality management system.
6. Start Training
ISO 9001 requires organisations to identify employees awareness, competence and training needs within the scope of QMS. Employee training is essential to help them understand the need for QMS implementation and certification, how it will affect their work and the consequences of non-conformance.
Training programs should be customised to the specific needs of different job roles, covering topics such as quality policy, objectives, procedures and responsibilities. Training your employees sooner rather than later will also help with the implementation process.
7. Develop Documentation
As per the ISO 9001 requirements, organisations are required to develop and control documentation related to the Scope of Quality Management System, Quality Policy, Quality Objectives and Procedures for the control of outsourced processes.
In addition, ISO 9001:2015 also includes requirements for various other documents and records needed to be developed, managed and controlled by the organisation. A robust document management system will help establish document creation, review, approval, distribution and control procedures. This system will also ensure that relevant documents are accessible to authorised personnel, updated regularly and securely maintained.
8. Implement the QMS
Once the QMS has been defined, it is time for implementation. The implementation phase involves introducing the new policies, processes and procedures within the organisation and helping employees adapt to them seamlessly.
However, it is not necessary to implement the system only when it is fully developed. As you go on defining each process, you can start implementing and training employees to save time and resources. This will also help identify gaps within the implementation and allow you to address them quickly.
9. Conduct Internal Audits
Internal audits are a vital tool for monitoring compliance with ISO 9001 regulations and identifying opportunities for improvement. Before having external audits by the certification bodies, conducting internal audits and management reviews will help you ensure the system's adequacy, suitability and effectiveness.
It will help find gaps between the standard requirements and existing processes. If there are any non-conformances, they can be handled promptly by corrective actions.
10. Seek Certification
Once the QMS is operational for three to six months, you can initiate the certification process from a nationally accredited certification body. The initial certification will be done in two stages- a document and readiness review, performed on-site and the final audit. The certification is awarded after a successful audit.
In Conclusion
Achieving ISO 9001:2015 certification requires a clear plan, commitment and systematic approach. By following these 10 steps, organisations can effectively navigate the ISO 9001 implementation process and position themselves for successful certification.