While an internal audit is an integral box to check during ISO certification, it's also one of the most effective ways to keep your quality management system (QMS) in shape. It helps you verify whether processes are working as planned, aligned with your objectives, and fully compliant with ISO 9001.
At its core, an internal audit is a structured, independent review of QMS activities. It measures how well your system conforms to planned arrangements and ISO requirements. When done right, it gives you early visibility into issues and supports continuous improvement.
However, the benefits of an internal audit depend on timing. If your internal audit frequency ISO 9001 is too low, you risk missing critical issues. If it's too high, audits become a burden: costly, repetitive, and hard to manage. Getting the frequency right is a balancing act between risk coverage and operational efficiency.
So, how do you decide how often to audit without overwhelming your team or falling behind on compliance? Let's understand ISO audit intervals and how to build a schedule that actually works.
How Often Should Internal Audits Be Done for ISO Compliance?
One of the most common questions asked during ISO implementation is: How often should ISO audits be done? The ISO 9001 standard doesn't provide a fixed answer. It doesn't mandate quarterly or annual internal audits. Instead, it expects organizations to take a risk-based approach that reflects their specific operations and challenges.
What ISO 9001 Says:
ISO 9001 requires internal audits to be conducted at "planned intervals" but leaves the actual timing up to you. That means ISO audit intervals should be determined based on:
- The importance of the process being audited
- The results of previous audits
- Operational changes or identified risks
This is what this kind of internal audit planning would look like in practice:
- High-risk processes: audit every quarter
- Low-risk, stable processes: audit once a year
- After a major non-conformance: audit immediately after corrective action
Internal audits aren't a substitute for external audits; they're your internal control. When used correctly, they support ISO compliance management and highlight issues early. Poor scheduling or long gaps between audits can lead to unnoticed process failures. Correctly timed internal audits can improve business performance.
Internal Audit Planning and ISO Requirements
Effective internal audits begin with smart planning. ISO 9001 expects you to plan audits systematically. Clause 9.2 outlines the core internal audit ISO requirements, and getting these right is essential for maintaining both compliance and performance visibility.
What ISO 9001 Clause 9.2 Requires
Here's what you need to cover under Clause 9.2:
- Planned intervals: You must define when audits will be conducted. These intervals should be documented and based on operational needs.
- Objectivity and impartiality: Auditors must be independent of the processes they are auditing to avoid conflicts of interest.
- Competence: Auditors should be trained, experienced, and familiar with both ISO 9001 and the QMS being audited.
- Documented results: Findings must be recorded clearly and made available to relevant stakeholders for corrective action and follow-up.
Meeting these internal audit requirements ensures that audits help you identify real gaps and prevent system drift.
What Should Internal Audit Planning Include?
A solid internal audit planning process helps you structure your audit activities in a way that delivers value. At a minimum, it should define:
- Scope: What process or department will be audited?
- Criteria: What standard, procedure, or regulation will it be measured against?
- Methods: Will the audit include interviews, document reviews, sampling, or site inspections?
Your audit plan should also consider process maturity, history of non-conformities, customer complaints, or any significant changes in operations.
How ISO Audit Checklists and Tools Help
Using an ISO audit checklist standardizes your planning and reduces human error. However, checklists alone aren't enough. Modern tools like Effivity take planning further by letting you:
- Assign audits to qualified personnel
- Set custom frequencies based on risk
- Track past findings and corrective actions
- Automate reminders and reporting
This level of structure simplifies your entire process, makes compliance easier, and aligns every audit with your broader QMS objectives.
How to Create an ISO 9001 Internal Audit Schedule
Building an effective ISO 9001 internal audit schedule requires a risk-based approach, resource planning, and the flexibility to adapt over time. Here are the steps to get started:
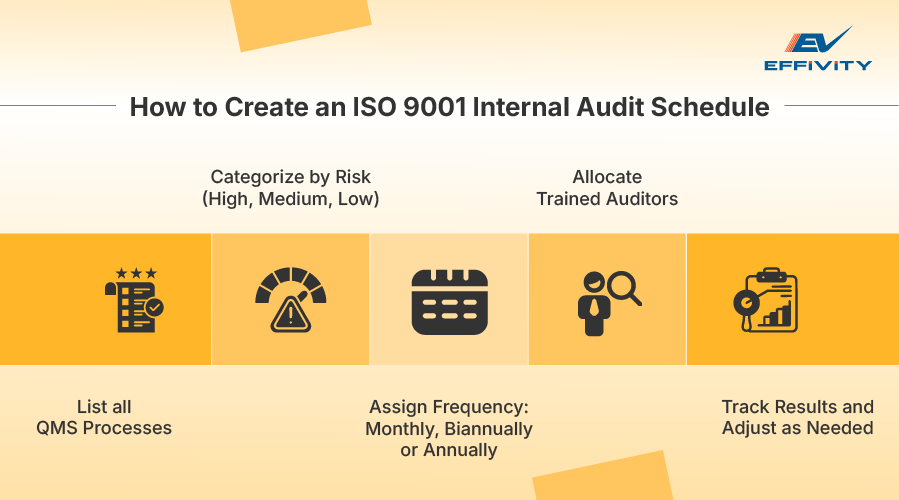
1. List all ISO processes: Start with a full inventory of QMS processes: document control, procurement, production, training, etc.
2. Categorize by risk or criticality: Assess each process based on customer impact, regulatory exposure, and history of non-conformities.
3. Assign frequency: Use risk levels to decide timing.
- High-risk: monthly or quarterly
- Medium-risk: biannually
- Low-risk: annually
4. Schedule auditors and resources: Assign trained, impartial auditors to each process and ensure the availability of supporting documentation.
5. Track and adjust: Use audit results to update the schedule. Processes with repeated issues may need more frequent reviews.
Audit Frequency Best Practices for ISO 9001
There's no universal formula for how often to audit, but there are smarter ways to decide. Done well, internal audits drive accountability, support continual improvement, and directly contribute to quality goals.
Here are four practices that help set the right audit rhythm.
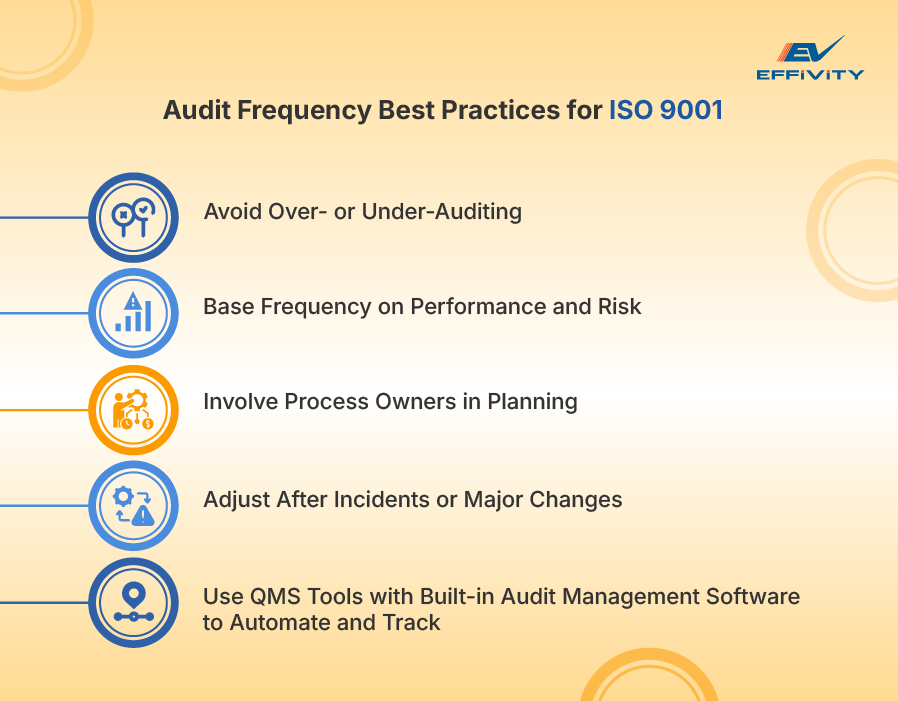
1. Don't Over-Audit or Under-Audit
Auditing too frequently ties up resources without adding value. Auditing too infrequently increases the risk of missed issues. Find the middle ground. Use past audit data, non-conformity trends, and process maturity to guide how often each area should be reviewed.
2. Let Performance and Risk Drive Frequency
Link frequency to actual performance. A process with frequent non-conformities or customer complaints should be audited more often. Stable, low-risk areas can be reviewed less frequently. This risk-based approach keeps your audit program focused and lean.
3. Involve Process Owners in Frequency Planning
Department heads understand their process cycles, peak workloads, and operational risks. Including them in planning makes your audit schedule more realistic and aligned with business needs.
4. Adjust Based on Change or Incidents
Post-incident reviews, major operational changes, or new regulations should trigger updates to your audit intervals. Modern QMS software solutions can suggest these adjustments automatically, keeping your schedule relevant without constant manual oversight.
5. Use Tools to Simplify Planning
Manual tracking is prone to gaps. A QMS software automates scheduling, sends reminders, and updates risk profiles over time. It's built-in Audit Management Software also generates reports and audit logs, helping you stay audit-ready year-round.
Bring Structure and Consistency to Internal Audits with Effivity
ISO 9001 offers flexibility when it comes to internal audits, but that flexibility still requires consistency, planning, and documentation. Defining your internal audit frequency ISO 9001 correctly involves using data, risk, and process maturity to guide decisions.
Manual planning often leads to missed follow-ups, scattered records, and audit schedules that don't reflect current risks. Without the right tools, your ISO 9001 internal audit schedule can quickly become outdated or unbalanced.
Effivity simplifies internal audits with a system built around ISO logic. You get:
- Pre-configured ISO audit templates
- Mapping of your custom internal audit requirements
- Automated scheduling based on risk
- Dashboards to track status, overdue audits, and findings
Book a free consultation to see how Effivity helps you run smarter, more consistent internal audits across your QMS.