The success and growth of any business ultimately come down to the quality of the product and service it provides. In doing so, the ISO 9001 standard is critical in defining the best practices for quality management within an organization.
ISO 9001 standard defines the requirements for QMS to help organizations streamline their processes, be more efficient, and achieve better product and service quality. Compliance with this standard is important to demonstrate commitment to quality and customer excellence.
However, ISO 9001 is often misunderstood as a standard requiring extensive documentation. While yes, the standard requires several documents for the quality management system to be effective, the essence of ISO 9001 compliance lies far beyond the paperwork.
It is all about fostering a culture of quality, continuous improvement, and customer satisfaction within an organization. This article delves into the true nature of ISO 9001, highlighting its core principles and holistic approach.
The Misconception of Documentation
There is a prevalent misconception about ISO 9001 that it heavily prioritizes documentation. While documented information is essential, it is not the sole focus.
Documentation is critical because it helps organizations ensure that the processes, procedures, and responsibilities are communicated and understood by the stakeholders involved. It also allows the process to be executed in an effective way that helps achieve its intended objective.
Most of all, records and documents need to be captured and maintained to ensure appropriate evidence and traceability where required.
Herein, several factors will define the documentation you will need to maintain within the QMS system. These include the level of automation with QMS software and the competence of the people involved in implementation and management.
The 2015 revision of the standard, ISO 9001:2015, has brought significant changes, emphasizing risk-based thinking, leadership engagement, context of organization, and process approach within QMS over exhaustive QMS documentation requirements.
The Real Focus of ISO 9001 Standard: Quality Management Principles
ISO 9001 is built on seven quality management principles that guide organizations toward operational excellence.
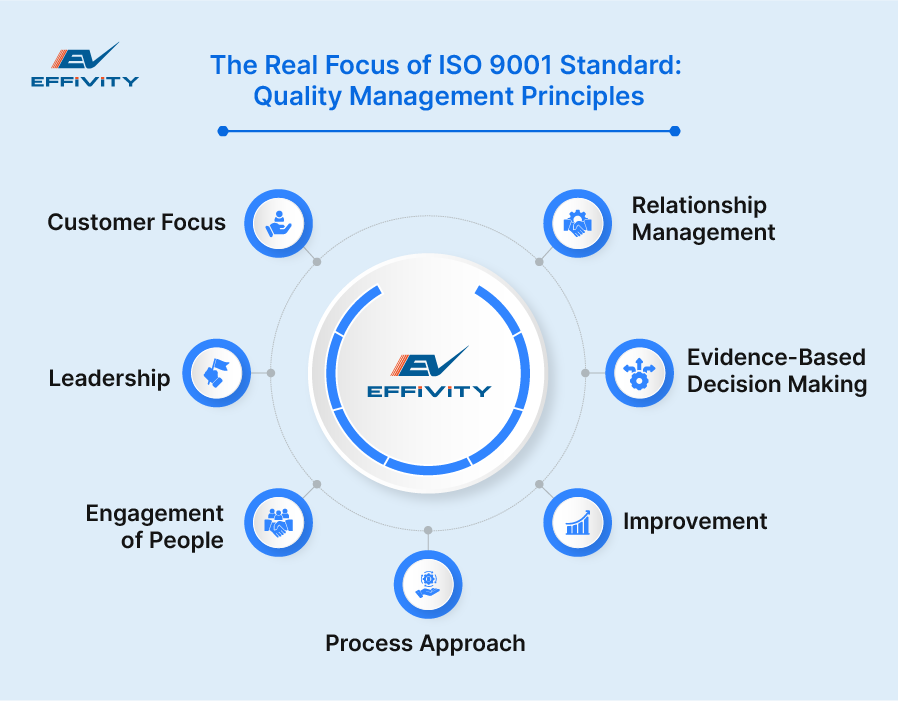
1. Customer Focus
The primary goal is to meet and exceed customer expectations. Organizations must understand customer needs, anticipate their future requirements, and strive to maximize customer satisfaction.
2. Leadership
Strong leadership is crucial for establishing QMS effectiveness and defining the objectives. Leaders at all levels need to create a quality-first culture within the organization, communicate their quality processes and policies, and ensure the availability of resources for successful QMS implementation.
3. Engagement of People
Competent, empowered, and engaged employees at all levels are essential for the organization's capability to create and deliver value. The employees must understand the value of implementing a QMS, and their contributions be recognized to foster a culture of quality.
4. Process Approach
Managing activities as processes helps in achieving consistent and predictable results. The process approach involves understanding and managing interrelated processes as a system, contributing to the organization's overall efficiency and effectiveness.
5. Improvement
A major objective of the organization should be continual improvement. Adopting this principle leads to enhanced performance, capabilities, and competitive advantage.
6. Evidence-Based Decision Making
Decisions based on data analysis and evaluation are more likely to produce desired results. ISO 9001 encourages the use of accurate and reliable data for decision-making.
7. Relationship Management
An organization's ability to create value is enhanced by managing relationships with interested parties, such as shareholders, customers, or suppliers. Nurturing these relationships that impact the organization's performance can help achieve continuous success.
QMS is a Continuous System
A fundamental aspect of achieving QMS objectives is to create the right amount and type of documentation and update it regularly. Further, these documents should be clear and easy to understand.
Think of the necessary QMS documentation as an integral part of your everyday operations. If it feels like an extra step, it's likely to be neglected until an audit is conducted, which can be highly inefficient and lead to errors.
However, when it comes to developing QMS documentation and ISO 9001 documentation control, one of the biggest challenges is determining where to begin. You might wonder how many documents you need, what they should look like, and what details to include for authorization and version control.
This is where QMS software like Effivity can be incredibly helpful in minimizing the guesswork. It offers document templates for ISO 9001 with fields for authorization wherever required. Additionally, version control happens automatically in the background, so you don't have to worry about it.
But that's not it. Once you have the template, the next challenge is to figure out what details need to be included within the documents. Effivity makes this easy, too, by offering context and suggestions for every field.
Integrate Your Management System into Your Processes
Achieving ISO certification means more than just meeting the standard's requirements. It is also about using the quality management system to improve your business processes. However, when you want to implement more than one ISO standard, things can get complicated. You might face issues like duplicated content or conflicting objectives.
To avoid these pitfalls, it's crucial to integrate your documentation seamlessly into your everyday activities. This approach ensures that documentation is always up-to-date and relevant, rather than a last-minute task before an audit. Using tools like Effivity's integrated management system simplifies the documentation process, making it more manageable and effective.
With an integrated management system, you can-
- Avoid duplicate documents
- Reduce overall risk
- Discover conflicting objectives and integrate them
- Create a formalized system out of informal processes
- Maintain compliance with various standards seamlessly
- Allow the organization to achieve its goals
Effivity's integrated management system software significantly reduces duplication and costs by providing you with the content you need to start or expand on within your existing QMS / EMS or OHSAS system.
The software combines many business components into one unified system, streamlining processes and management, business objectives, audits, and continual improvement initiatives.
In the End
ISO 9001 compliance is much more than maintaining documentation. It's about embedding a quality culture within the organization, focusing on customer satisfaction, continuous improvement, and effective process management.
While the documentation serves as a tool to support ISO 9001 objectives, the real focus remains on creating value through a robust and dynamic quality management system.