ISO 9001 is incomplete without measurement and monitoring. These are unavoidable activities if your organization wishes to consistently meet various quality standards and achieve ISO certification.
Measurement and monitoring go beyond just ISO compliance. It helps you track performance, identify processes and areas that need improvement, and verify if the corrective actions you take are effective.
In short, measurement and monitoring helps you make better decisions. It diminishes the risk of errors and ensures that you are able to deliver consistent quality at all times.
In this article, we explore how measurement and monitoring can help you make better decisions for your organization’s products and processes, and how a Quality Management Software can help you with this.
Measurement vs. Monitoring: Key Differences
Measurement and monitoring might seem similar, but they serve different purposes.
Measurement focuses on quantifying specific aspects of your processes. For example, you measure production time, defect rates, or customer satisfaction scores. These numbers give you a clear, objective understanding of how well your processes are performing.
Monitoring, on the other hand, is about keeping an eye on processes over time. It’s like a continuous check-up. You monitor to ensure that everything stays within acceptable limits.
1. Frequency and Timing
Measurement often happens at specific intervals. You might measure performance at the end of a production cycle, after a project milestone, or during a scheduled audit.
Monitoring is ongoing. For this you could be using a QHSE Management Software dashboard that you glance at regularly to ensure everything is running smoothly. In many cases, monitoring happens in real-time.
2. Actionability
Measurement is highly actionable because it provides concrete data that can drive decisions. If your measurement shows that defect rates are rising, you can investigate the cause and implement corrective actions.
Monitoring is more about prevention and control. It helps you maintain consistency and avoid deviations before they become significant problems.
Measurement and Monitoring: Product Quality
Ensuring product quality is a non-negotiable priority for any organization aiming for ISO 9001 certification. Measurement and monitoring help you confirm that your products consistently meet customer requirements and conform to planned specifications.
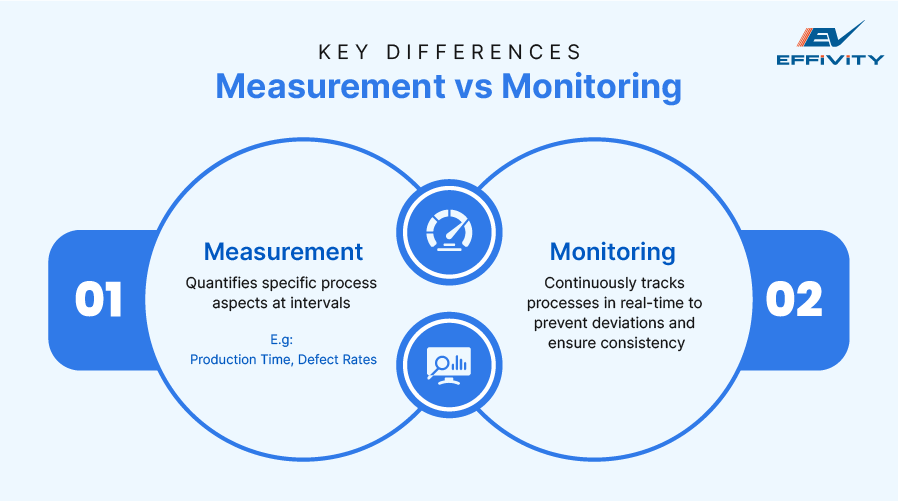
Measurement and Product Quality
Measurement quantifies specific characteristics of your products. It’s how you determine if a product’s weight, size, or performance aligns with the set standards. It ensures that there are no deviations, and that quality is maintained in each item.
For example, measuring a product’s dimensions ensures it matches the blueprint or design specifications.
Monitoring and Product Quality
While measurement gives you specific data points, monitoring provides a continuous overview of the process. It helps you keep an eye on your manufacturing processes and track changes that may cause product quality issues.
A good example of this is the temperature levels in food productions. When you monitor temperature levels, you will be able to notice if there are any changes that may affect the quality of food produced.
Monitoring can also help you anticipate problems with the help of trend analysis.
Measurement and Monitoring: Process Efficiency
Process efficiency is another facet of achieving ISO 9001 certification. Measurement and monitoring are your best tools to ensure your processes run smoothly. Efficient processes save time, reduce costs, and increase overall productivity.
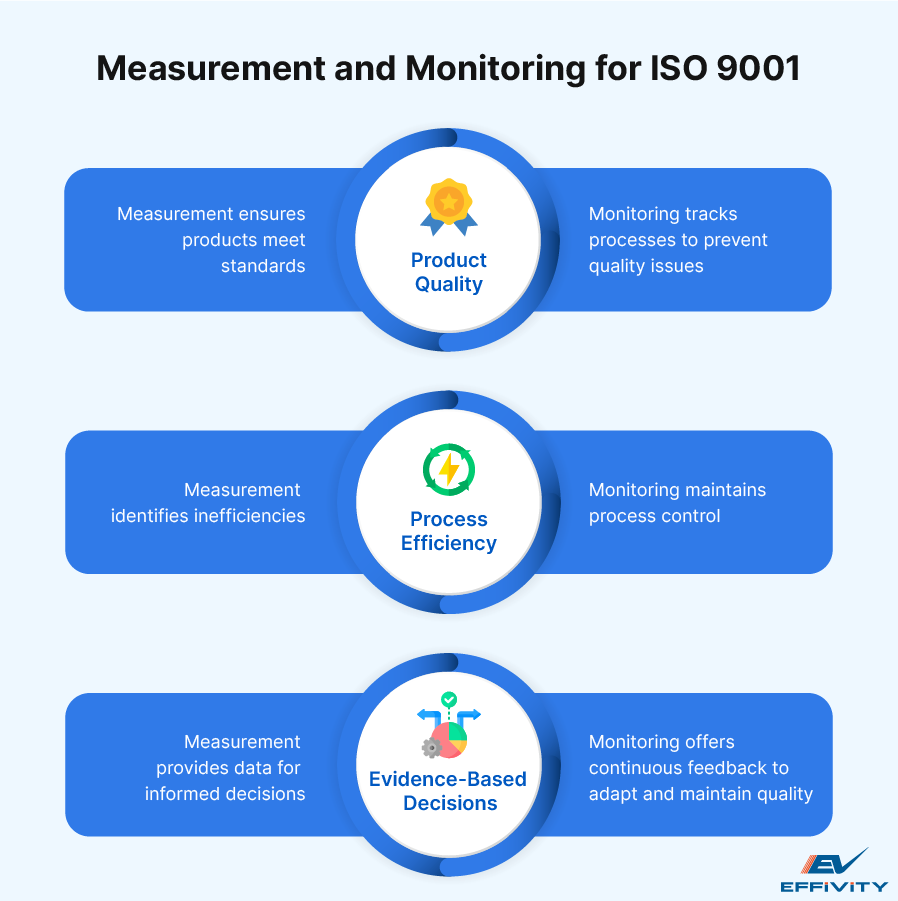
Measuring Process Efficiency
Measurement in process efficiency involves assessing specific aspects of a process to determine its effectiveness.
For example, you may measure the time taken to complete a certain task to identify bottlenecks, or you may track the amount of resources used to pinpoint areas for cost savings.
Measuring helps you obtain metrics that provide a clear picture of how well your process is performing and where you can apply measures to improve.
Monitoring for Process Control
Monitoring ensures that your processes remain under control and continue to perform as expected. With monitoring, you can keep a constant eye on your key performance indicators to detect any deviations from the norm.
Some examples of monitoring in process control include real-time output tracking to monitor the output rate of a production line or monitoring the gradual increases in energy consumption of a machine that can signal the need for maintenance.
Monitoring helps you achieve process stability and enables you to spot potential problems early. This way, you can take corrective actions before they escalate into larger, costlier issues.
Evidence-Based Decisions with Measurement and Monitoring
Evidence-based decision-making is a core principle of ISO 9001. Measurement and monitoring shine in this regard as they provide you with the hard data necessary to make informed and objective decisions on a daily basis. Informed decision-making helps your organization achieve its quality goals.
How Measurement Supports Evidence-Based Decisions
Measurement provides the quantitative data that forms the foundation of evidence-based decision-making. When you measure aspects of your processes or products, you gather the information necessary to evaluate performance against standards and objectives.
Measurements allow you to make decisions based on facts rather than assumptions. If data shows a process is underperforming, you have the evidence needed to justify changes, such as:
- Reallocating Resources
- Adjusting Process Parameters
- Investing in New Equipment
How Monitoring Supports Evidence-Based Decision Making
Monitoring complements measurement by providing ongoing feedback. It helps continuously observe processes to ensure they remain on track. Monitoring helps you make decisions that are responsive to current conditions. This adaptability is crucial in maintaining high levels of quality management and efficiency.
Final Thoughts
The true power of measurement and monitoring lies in their integration. When used together, they provide a comprehensive view of your organization’s performance. Measurement offers concrete data to help you understand where you stand, whereas monitoring provides continuous feedback to keep you on the correct path.
Incorporating measurement and monitoring into your quality management system is essential for making evidence-based decisions that drive continuous improvement.
An easy way to do this is by using the Measurement and Monitoring module of Effivity’s Quality Management Software. This easy to use, scalable and adaptable software solutions helps you meet your quality objectives and keeps you on the track to achieving ISO 9001 compliance.