ISO 9001 is one of the key international standards that lay down the key requirements for quality management systems. Organisations of all industries and sizes can rely on ISO 9001 standards to organise their processes, improve efficiency and demonstrate the ability to provide quality products and services to their customers.
In 2015, the International Organisation for Standardisation revised the ISO 9001 QMS standard to introduce new terminology, emphasise risk-based thinking, enhance leadership requirements and more. One of the aims of ISO 9001:2015 was to improve the requirements for addressing QMS change management.
What is Change Management?
Change management is the systematic process of planning, managing and implementing change in an organisation from start to finish. The aim of a change management system is to put strategies in place that will help effect change, control the change and help people in the organisation to adapt to the change.
These changes could vary from introducing a new technology to changing the organisational hierarchy. No matter the type of change, change management gives you more control over the planning and implementation processes, allowing you to monitor and record the success of the change.
ISO 9001:2015 QMS Change Management
The updated ISO 9001:2015 standard emphasises the organisation’s ability to adapt and respond to change, encouraging a proactive approach to managing changes impacting QMS. In the ISO 9001:2015 standard, QMS change management is specifically mentioned in 4 clauses of the standard. These include-
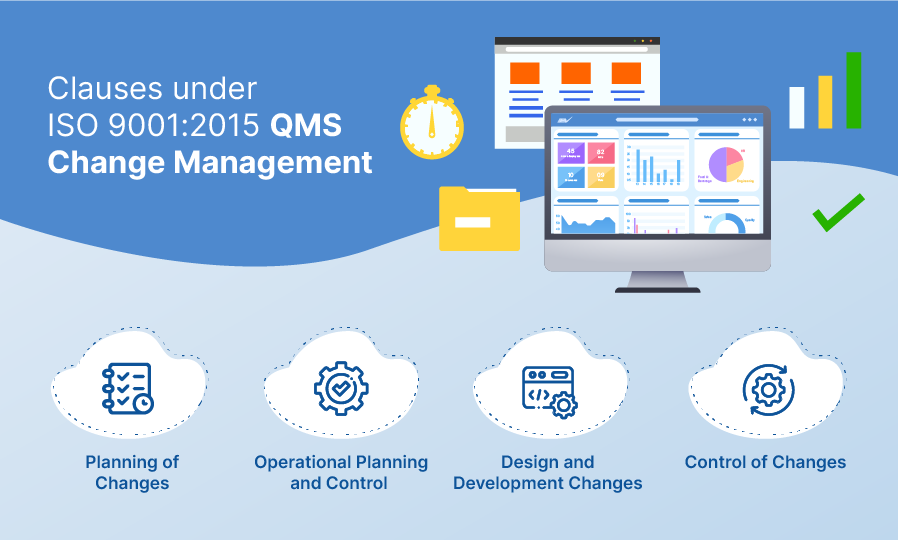
- 6.3 Planning of Changes: Any changes to the QMS must be carried out in a planned and systematic manner.
- 8.1 Operational Planning and Control: The organisation must take a strategic approach to control planned changes, review the implementation of changes and take the necessary steps to mitigate any adverse effects.
- 8.3.6 Design and Development Changes: This requires the organisation to review and control the identified changes in the design and development process to ensure quality and minimise product non-conformance.
- 8.5.6 Control of Changes: The organisation must review and control changes within its quality management systems for production or service provision to ensure conformity with the requirements.
Why is Change Management Important?
A change in the QMS can be a result of various factors, such as-
- Customer complaints or feedback
- Employee feedback
- Innovation
- Product failure
- Determined risk or opportunity
- Internal audit results
- Identified non-conformity
- Management review results
Once you mandate changes, having a plan to control, monitor and record change will allow your organisation to set clear goals for change processes, encourage employees to navigate the changes faster and enable success. This is why it has become a core requirement of the organisation’s QMS that these changes be successfully managed and controlled.
With the new requirements of change management, the ISO 9001:2015 aims to improve the strategies that address change at both operational and system levels. This provides a strong basis for QMS using quality management software to determine the strategic direction of the company.
Once an organisation has specified its processes and identified the risks and opportunities, a change in resources, activities, inputs, or outputs is necessary to realise the benefits of new opportunities identified. Here, managing these changes becomes increasingly important in order to guarantee continued success.
What Constitutes a Change in the Organisation?
There are various things that can be a part of the change management procedure to help the organisation improve their QMS.
- Processes (inputs, outputs, controls)
- Communication with supply chain or customers
- Employee training
- Inspection
- Additional control for processes
- Documented information
- Employee competence
However, not all these changes are equal. While some have to be managed carefully, some can be ignored. To determine how to treat a change, businesses need to prioritise changes based on-
- Likelihood of the change recurring
- Consequences of the change
- Impact on interested parties
- Impact on quality objectives
- Impact on customers
How to Implement QMS Change Management?
No matter what processes, resources, people, or activities require a change, a change management lifecycle involves the following steps-
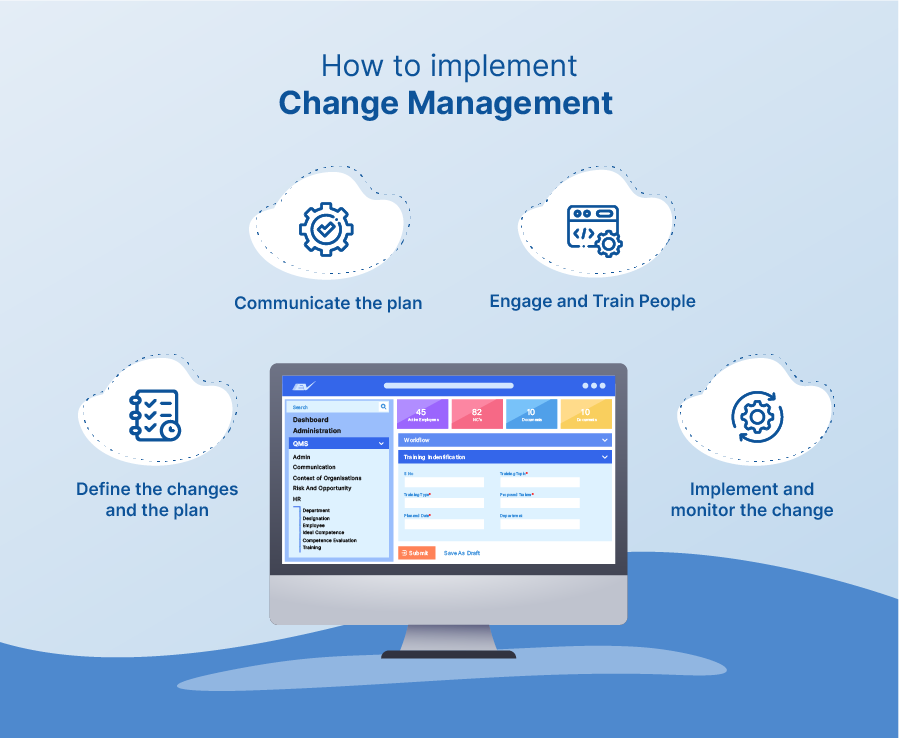
1. Define the changes and the plan
Start with defining the various aspects of the change. This includes defining what has to be changed, the reason for the change, when the change will occur and whom it will impact. Additionally, organisations must design a plan for how the change will occur and be managed. A change plan will typically include defining tasks, responsibilities, budget, authorities, resources and information needed.
2. Communicate the plan
Next, it is important to design a communication plan to ensure that all the relevant stakeholders who are impacted by the change know what is happening and why. Craft a message taking into consideration the risks and consequences of the change and communicate it with different parties, including employees, customers, suppliers and other interested parties.
3. Engage and train people
No change can be successful unless it is supported with proper employee training to ensure a seamless transition. An effective training program can help offer the necessary knowledge and skills to adapt to the change. In addition, appointing a team to review the plan and provide feedback can help streamline the implementation.
4. Implement and monitor the change
Finally, the change within the organisation must be executed. This has to be followed by regular monitoring and analysis to determine the success of the change implemented. Measure the effectiveness of the change, identify possible risks and make necessary adjustments to ensure careful planning and implementation of QMS change management.
Wrapping Up
ISO 9001:2015 offers a streamlined and proactive approach to QMS change management. Since poorly planned, uncontrolled changes can affect the quality and reliability of products and services; organisations must take the necessary steps to control QMS implementation with an effective operation management system.
Using an effective software solution, organisations can facilitate seamless change implementation, enhance communication and make the transition smoother for all the parties involved.