Monitoring, measuring, and analysing data within your QMS system is essential for ensuring the efficacy of your processes, products, and overall business performance. It is one of the key requirements of ISO 9001:2015 to ensure the QMS software meets the organisation's requirements.
Effective data analysis allows organisations to identify trends, assess performance, and make informed decisions to continually improve their quality management practices. However, for data measurement and analysis to succeed, you must have enough accurate evidence to assess a product or process properly.
This means you must analyse the QMS data system to make it useful and meaningful for the management to drive data-driven decisions. Here, deciding which data should be analysed is as important as deciding which data should be collected.
Let's explore what QMS data your organisation can analyse, monitor, and measure to facilitate continual improvement.
Why Should You Be Analysing Your Data?
Within the ISO 9001:2015 standard, monitoring and measurement are two key elements of an effective QMS that require you to
- Plan resources to ensure that the measuring and monitoring processes are effective.
- Rely on evidence to make decisions.
- Use the rational evidence derived from these processes to drive continual improvement.
However, per ISO 9001 standards, simply monitoring and measuring QMS data isn't enough. Organisations must also analyse this data to determine if their quality management system is suitable and effective. This will allow them to identify areas for continual improvement.
Importance of Data Measurement, Monitoring, and Analysis
Here's why these processes are crucial:
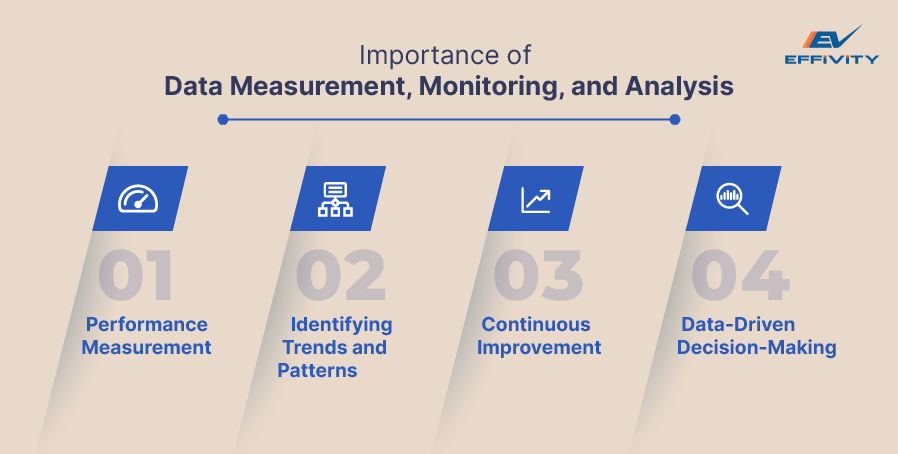
1. Performance Measurement
Measuring and monitoring QMS system data allows organisations to assess the performance of their quality management processes and systems. By tracking KPIs, such as defect rates, customer satisfaction scores, and process efficiency, companies can identify areas for improvement and maintain compliance with ISO 9001 standards.
2. Identifying Trends and Patterns
QMS data system analyses enable organisations to identify trends, patterns, and recurring issues that may impact product quality or process efficiency. They can leverage statistical methods and data visualisation techniques to determine non-conformances and uncover insights into the root causes of issues. This will enable them to implement targeted corrective actions and prevent future occurrences.
3. Continuous Improvement
One of the key requirements of QMS implementation and regulatory compliance is that organisations must demonstrate continuous improvement. With a comprehensive measurement system that evaluates performance metrics and analyses data trends, organisations can identify opportunities to optimise processes product innovation, and reduce costs.
Continuous improvement efforts based on data insights allow companies to enhance customer satisfaction, achieve higher operational efficiency, and maintain a competitive advant in the market.
4. Data-Driven Decision-Making
Organisations need to measure the QMS performance based on data to ensure it performs as designed. So, for each process, comparing the results to expected results and analysing this data will help organisations make informed strategic decisions and resource allocation.
With regular QMS data analysis, management teams can gain valuable insights into the effectiveness of quality management initiatives, prioritise improvement efforts, and allocate resources where they are most needed. It will also allow them to take corrective actions promptly to ensure that the QMS stays aligned with the business goals and objectives.
4 QMS Data Systems to Be Analysed
The ISO 9001 standard mentions four specific areas of important data sources organisations must analyse.
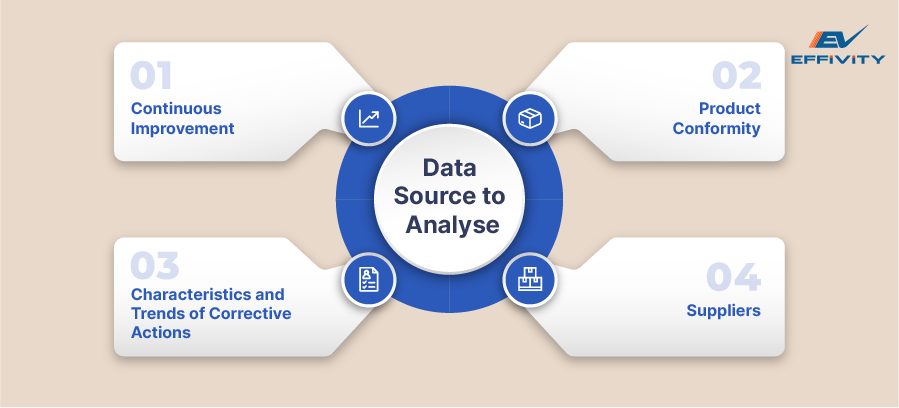
1. Customer Satisfaction
Customer satisfaction is a critical factor that can help a business determine the success of its product or service. After all, it is not about how you think you've met customer needs or how good your services are; it is about how your customers perceive you. As a result, it is also one of the most difficult factors to measure and monitor.
However, there are several ways to connect with your customers and get their feedback. Here's how you can do it-
- Track customer returns
- Monitor customer comments on social media
- Know how or what they are talking about your business on social media groups
- Monitor personal interactions with sales teams
- Monitor their feedback
Your company's survival may depend on how well you monitor and measure customer satisfaction and what steps you take to enhance it.
2. Product Conformity
One way to ensure your customers are happy and satisfied with the business is to ensure that your products and services meet their requirements. Start with identifying customers' critical needs and evaluating whether your product meets those needs. Look for any issues and define corrective actions to address them promptly.
In addition, you must also look at the legal requirements of the product to maintain compliance, as well as the internal requirements to ensure the product and services work.
3. Characteristics and Trends of Corrective Actions
It is a common saying that prevention is better than cure. This is especially true if you're looking to enhance the customer's perception of how well your company meets their needs.
To take a proactive approach to the QMS system and data quality management, you must identify trends when handling non-conformances and apply appropriate corrective actions to prevent future occurrences. It becomes easier to create a culture of improvement within the organisation once you adopt a problem-prevention approach and collect data accordingly.
For instance, you might identify a trend that operator errors are most often caused by a lack of training or changed working environments. Once you have identified this trend, it becomes easy to define the corrective actions to improve the situation and prevent the errors before they negatively impact products and services or their delivery.
4. Suppliers
Companies often rely on the performance of their suppliers to be able to meet their own customers' requirements. Then, monitoring and analysing supplier data can help organisations determine areas for improvement.
For example, organisations could work with suppliers to improve their delivery times by reducing the complexity of product requirements. This will help improve the company's ability to deliver products to their customers on time.
If you consistently work with your suppliers to improve how they work for you, it will allow you to improve your customers' quality of products and service.
Using Data Based on Evidence
When reviewing, monitoring, and measuring QMS data, organisations must look at two data sets – the data that shows if the processes are performing as expected and the data that can help them determine areas for improvement. Collecting and analysing data from areas that need improvement will not only enhance the organisation's overall efficiency but also improve their bottom line.