Quality Management has always been a non-negotiable requirement in nearly all industries and workplaces. When it comes to quality, there are many aspects to consider and track simultaneously. Without a proper system, this can lead to inefficiencies and be extremely time and resource intensive.
ISO 9001 gives you a reliable and structured framework for managing quality effectively. This standard is periodically reviewed and revised to ensure it stays relevant and effective as the industry practices and expectations constantly change. The latest version is ISO 9001:2015 and there are significant updates that enhance its applicability and focus.
Migrating from ISO 9001:2008 can be challenging as it involves substantial changes to existing processes and documentation. The new standard emphasizes risk-based thinking, a process-oriented approach and greater involvement from leadership.
In this article, we address how to migrate from ISO 9001:2008 to ISO 9001:2015. We provide a step-by-step guide to help you navigate the transition smoothly. Additionally, we explore how you can simplify this process using your quality management software.
ISO 9001:2008 vs ISO 9001:2015: Key Differences
Understanding the key differences between ISO 9001:2008 and ISO 9001:2015 helps with a smooth transition. These changes in the framework were made to improve flexibility, integrate risk-based thinking and ensure the standard's relevance in today's business landscape.
Here are the key changes that were made to the framework:
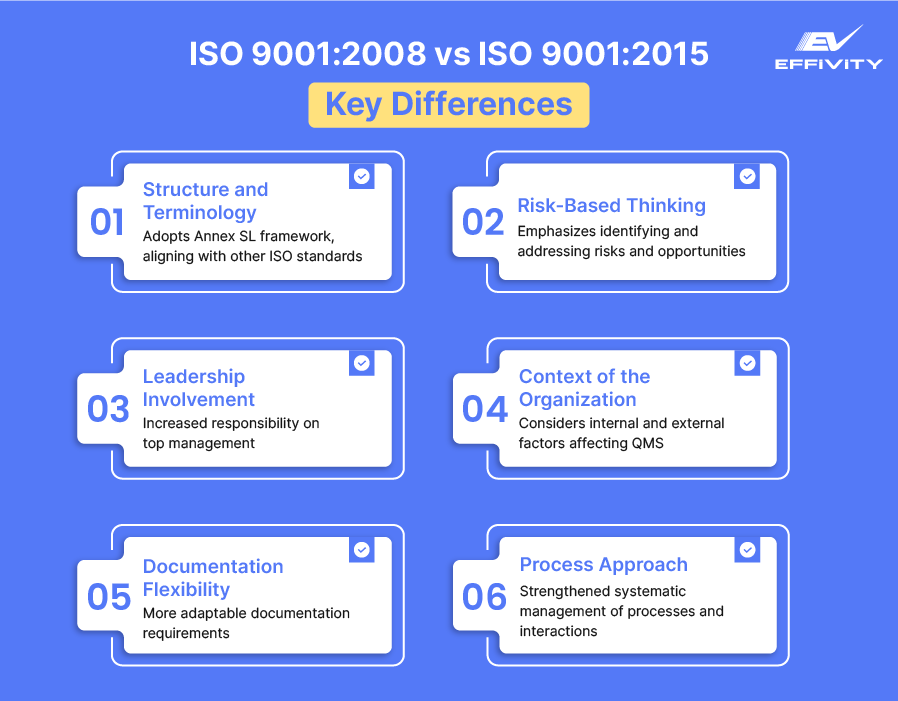
1. Structure and Terminology
ISO 9001:2015 adopts the Annex SL framework, aligning with other ISO standards for easier integration. The terminology has been updated to be more generic, making it applicable across various industries. This structured approach simplifies implementation and promotes consistency in your QMS.
2. Risk-Based Thinking
The 2015 version emphasizes risk-based thinking. You need to identify risks and opportunities that could impact your QMS. This proactive approach ensures potential issues are addressed before they escalate, enhancing overall quality and performance.
3. Leadership Involvement
ISO 9001:2015 places greater responsibility on top management. Leaders must actively engage with the QMS, align it with business strategies and demonstrate commitment. This involvement fosters a culture of quality throughout your organization.
4. Context of the Organization
You must consider the internal and external context of your organization and QMS. This involves analyzing factors like your organizational culture, market conditions, regulatory environment and technological trends. Understanding these elements helps in identifying risks and opportunities that can impact your QMS.
Understanding stakeholders' needs and expectations is crucial for tailoring your QMS to your business environment. Stakeholders include customers, suppliers, employees and regulatory bodies. This way, you ensure that your system remains relevant and effective.
5. Documentation Flexibility
ISO 9001:2015 offers more flexibility in documentation. The term "documented information" replaces "documents" and "records," allowing for a broader interpretation.
You can now determine the extent and format of documentation required, making it easier to manage and maintain. This approach ensures that documentation is relevant and streamlined to your organization's needs.
6. Process Approach
ISO 9001:2015 reinforces the process approach, requiring systematic management of processes and their interactions. This involves detailed planning, implementation and monitoring to ensure each process contributes to overall objectives.
Improving processes continuously helps achieve consistent and intended outcomes. This approach enhances efficiency and effectiveness and aligns with the standard's focus on delivering quality with consistency.
How to Conduct an ISO 9001:2015 Migration?
Moving to ISO 9001:2015 involves many steps and doing it manually can be challenging. You might face issues like extensive documentation updates and employee training. Using QMS software can simplify this process, making it more efficient and less stressful.
QMS software helps manage documentation, track progress and streamline communication. This ensures a smooth transition while maintaining compliance with the new standard. Here are steps you must follow to go through with the migration.
1. Gap Analysis
Conduct a thorough gap analysis to identify differences between your current system and ISO 9001:2015 requirements. Review existing processes, documentation and practices. Highlight areas needing changes to meet the new standards. This analysis provides a clear roadmap for what needs to be addressed, ensuring no critical aspects are overlooked during the migration.
2. Create an Implementation Plan
Develop a detailed implementation plan. Outline tasks, responsibilities and timelines. Assign roles to team members and set milestones. This structured approach keeps the migration process organized and on track. An implementation plan acts as a blueprint, guiding your organization through each step and ensuring that every aspect of the migration is covered.
3. Update Documentation
Revise your QMS documentation to align with ISO 9001:2015. Update policies, procedures and work instructions. Ensure that all documents reflect the new requirements and changes identified in the gap analysis. Accurate documentation is a necessity for compliance and gives employees a reference to understand the new processes and responsibilities.
4. Train Employees
Provide training to employees on the QMS upgrade. Ensure everyone understands the new standard, changes in processes and their roles in maintaining compliance. Well-informed staff help achieve a successful transition.
Training sessions should be comprehensive, addressing all aspects of the new standard to empower employees to effectively implement and support the updated QMS.
5. Implement Changes
Apply necessary changes to processes, documentation and systems. Monitor your progress regularly and address any issues that arise promptly.
Implementation should be systematic, with continuous monitoring to ensure changes are effective and aligned with ISO 9001:2015 requirements.
6. Internal Audits
Conduct audits to verify your compliance with ISO 9001:2015 periodically. Review processes and documentation to identify non-conformities. Use audit findings to make further improvements before the certification audit. Internal audits provide an opportunity to catch and correct issues early, ensuring the organization is well-prepared for the official certification process.
7. Management Review
Hold management review meetings to evaluate the quality management system upgrade. Discuss audit results, performance metrics and areas for improvement. Ensure top management is engaged and supportive of the transition process. Management reviews help align the QMS with organizational goals and demonstrate leadership commitment to quality management.
Final Thoughts
Migrating to ISO 9001:2015 is essential for maintaining a modern, effective Quality Management System. This transition ensures your organization stays competitive and compliant with current standards. While there can be many challenges in the ISO 9001 transition, addressing them through structured steps makes it manageable.
Using QMS software significantly simplifies the transition. It helps manage documentation, track progress and systematize communication, making the entire process more efficient and less stressful. With the right tools, you can ensure a smooth and successful migration to ISO 9001:2015.