It's no secret that customers are the lifeblood of any business. No customers simply means no business. A key aspect of attracting and retaining customers is focusing on the quality of the product or service the business offers.
Every business needs to ensure its products and services meet customers' requirements and prioritize their satisfaction. This is where ISO 9001 standard requirements are a potential game changer.
The ISO 9001 quality management system standard includes two dedicated sections requiring the QMS to implement processes to understand their products or services. These requirements deal with defining the requirements and then reviewing those requirements.
In this article, we'll explore in detail the product requirements in ISO 9001 that organizations need to meet within the quality management system.
Understanding ISO 9001:2015 Clause 8.2
Clause 8.2 of ISO 9001:2015 outlines the specific requirements for products and services. This clause ensures that organizations understand their customers' needs and expectations and consistently deliver products and services that satisfy those requirements.
This section is divided into various sections, focusing on communicating with the customers, determining the requirements for products and services, and reviewing those requirements to ensure that customer satisfaction is achieved effectively.
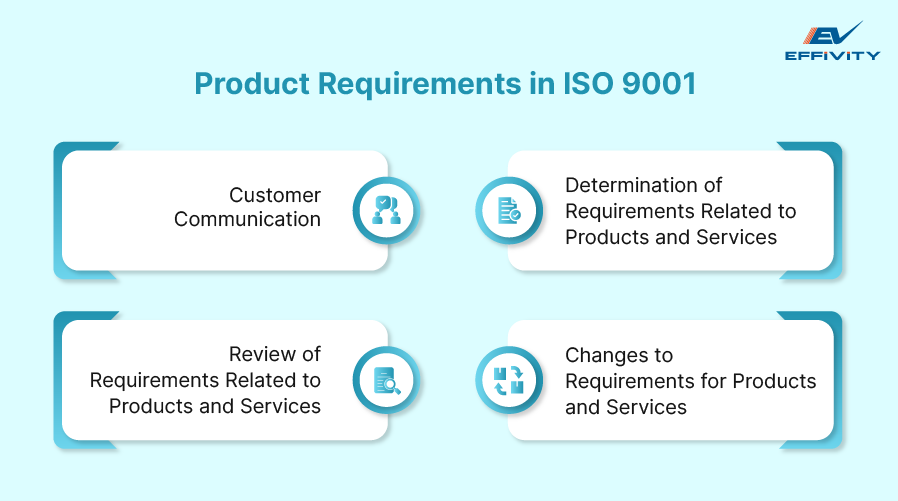
1) Customer Communication
Effective communication with customers is vital. This clause requires that organizations establish robust communication with customers regarding product information and handling inquiries, contracts, orders, changes, and customer feedback.
This ensures that the organization can clearly understand customer expectations and requirements and take the necessary actions to meet them. It also involves documenting processes for understanding and reviewing customer needs as well as maintaining detailed records of what the customer expects from your business.
2) Determination of Requirements Related to Products and Services
Organizations must determine and review all customer requirements before committing to supply products and services. Additionally, they must have the capability to fulfil these requirements.
However, determining product requirements is often harder than it first appears. Customer requirements can differ, from delivery requirements to after-sales services. Plus, there are always specific requirements that customers don't state, but these could be determined by what the product is intended for.
Further, it needs to determine the regulatory, statutory, and organizational requirements for its products and services. Most companies must meet specific legal requirements and additional ones they have established internally within their quality management software.
For instance, if you specialize in offering life preservers, the customer will require that it be a specific size and quality to achieve its intended use of keeping the person afloat. The legal requirements for life preservers may specify the material or color, while the company could identify that a robust and waterproof fabric should be used. The requirements from these 4 different areas would ideally be part of the product's design.
This is where it also becomes necessary to document the processing for determining product requirements, as it will ensure that you don't miss out on anything critical and limit the chances of customer dissatisfaction.
3) Review of Requirements Related to Products and Services
Before accepting an order or supply contract, it is essential to review the requirements to ensure the organization can meet them. This involves verifying all the customer requirements are mentioned clearly, including those not specified by the customer but necessary for the product or service.
Agreements to supply products or services to customers can take many forms, including submitting tenders and accepting orders or contracts. When the requirements are reviewed, it is also important to review and accept any changes to the original tender, order, or contract.
The review must ensure that all requirements are clearly defined, irrespective of where they come from. This also involves resolving any discrepancies within the requirements. If there are two types of requirements where the customer requirement does not align with the company's requirements, they should be discussed and resolved in time.
For instance, a customer might want a lightweight plastic part, but the company knows that a metal part is needed within the machinery due to excess wear.
In ISO 9001 product requirements, the final aspect of the review involves ensuring that the company is able to meet the requirements that have been defined. For instance, if the order quantity changes from 10 to 100 but the delivery time stays the same, the company might decide this is impossible. Since more time is needed to create the product or service, the same must be communicated effectively to the customer.
4) Changes to Requirements for Products and Services
Finally, it is crucial to manage changes to product and service requirements effectively. If the organization has identified any discrepancies in requirements in the previous step, it might result in certain changes.
For instance, an order could change and result in a new requirement that had not been considered previously. Suppose the quantity ordered could increase from 10 to 100, but the longer delivery time had not been considered previously. Such changes need to be identified and communicated proactively.
As always, it is important to maintain proper records of reviews and order acceptance. Changes should also be communicated to employees who are responsible for implementing the changes.
Although a formal review of orders may be impractical in some cases, such as online sales, a review of product information in advertising materials may be needed, as it will be used to place the order.
Improving Customer Satisfaction
Adhering to the ISO 9001 product requirements brings numerous benefits to the organization, including enhanced customer satisfaction.
By consistently meeting customer requirements, organizations can improve customer satisfaction, leading to repeat business and positive word-of-mouth. Improved quality and efficiency result from a clear understanding and documentation of requirements, leading to better products and services and improved operational efficiency.
Ensuring compliance with statutory and regulatory requirements also helps organizations avoid legal issues and penalties. Identifying and addressing requirements effectively helps mitigate non-compliance and customer dissatisfaction risks.
Additionally, organizations that adhere to ISO 9001 standards can market their commitment to quality, gaining a competitive edge in the marketplace.