Organisations across industries are constantly striving to improve their quality management processes and systems to stay ahead of the curve. In an era where customers and stakeholders expect quality in business operations and results, effective quality control plays a pivotal role in ensuring customer satisfaction, operational efficiency and overall business success.
With the advent of technology and the abundance of data available to businesses, data analytics plays a key role in improving quality management systems. Quality assurance analytics offers valuable insights to organisations that can help them identify performance gaps and potential issues, mitigate risks and improve performance.
This article will look at the role and benefits of analytics in improving quality management.
Why is Data Analytics Important in Quality Management?
No matter which industry, the role of data in quality management cannot be understated. It helps in decision-making, understanding patterns and evaluating the organisation's performance as well as areas of improvement. In the context of quality control and management, organisations can track key quality metrics and collect extensive data such as quality costs, defect density, yield, scrap, compliance metrics, customer satisfaction and more.
However, any historical or real-time data is useful when carefully analysed to generate meaningful insights. Organisations can employ a number of statistical techniques, such as ISO gap analysis or Six Sigma analysis, to identify issues, correlations and root causes that can lead to defects and take the necessary actions to improve quality management and enhance process efficiency.
The Role of Analytics in Improving Quality Management
Effective quality management analytics using data offers several benefits to organisations looking to improve their quality monitoring and processes. Let's explore them in detail.
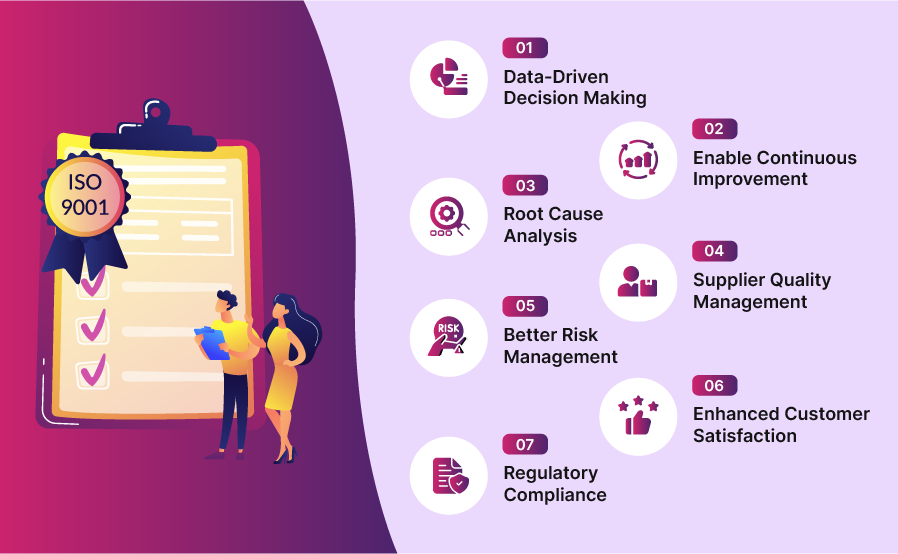
1.Data-Driven Decision Making
A key benefit of using analytics in quality management is that it offers the ability to make informed, data-driven decisions. Analytics empowers organisations to base their decisions on valuable insights extracted from real-time data.
By analysing QMS monitoring and measurement data related to quality issues, defect rates, customer feedback and production processes, organisations can identify underlying causes and proactively address them. For instance, predictive analytics can anticipate potential quality issues before they occur, allowing organisations to improve and streamline their processes and avoid costly defects.
2. Enable Continuous Improvement
Manual quality inspection and control processes can be time-consuming and labour-intensive. However, through continuous monitoring and analysis of quality-related metrics using digital tools,organisations can automate and speed up quality checks, identify areas for improvement and facilitate continuous improvement.
Whether it's optimising manufacturing processes to minimise defects, refining product designs based on customer feedback, or streamlining supply chain operations to enhance efficiency, analytics offer the insights you need to drive continuous improvement initiatives. Moreover, by using real-time analytics, organisations can quickly respond to quality issues and work to enhance customer satisfaction.
3. Root Cause Analysis
Identifying the root causes of quality issues is a key aspect of undertaking effective corrective actions and preventing recurrence. With QMS software's dashboard reporting capabilities, businesses can identify patterns and relationships with data visualisation and encourage root cause analysis.
By analysing factors such as production, supplier performance, environmental conditions and more, organisations can recognise the cause behind quality problems. Furthermore, advanced analytics techniques, like machine learning and artificial intelligence, can automatically detect patterns and correlations that might be overlooked manually, thereby enhancing the accuracy and effectiveness of root cause analysis.
4. Supplier Quality Management
When it comes to the quality of your products and services, organisations cannot ignore the role of suppliers and partners. Quality assurance analytics plays a crucial role in supplier quality management by helping organisations evaluate supplier performance, identify high-risk vendors and optimise sourcing decisions.
With access to data related to supplier quality, delivery times, pricing trends and compliance metrics, organisations can make informed decisions about supplier selection, contract negotiations and relationship management. Not to mention, analytics can help organisations anticipate potential supply chain disruptions in advance. This allows them to proactively mitigate risks, ensuring process efficiency and business growth.
5. Better Risk Management
Robust QMS system software features advanced analytics systems that monitor, measure and report real-time data from various processes, such as plant machinery or product documentation, to stay on top of quality management. These systems can proactively detect risks and irregularities in various manufacturing or operational processes that can affect the quality of the product.
For instance, the system may alert the organisation of any potential safety hazards in the production process that can hamper the quality. As a result, businesses can prevent quality issues and take the necessary steps to mitigate risks that may have occurred otherwise.
6. Enhanced Customer Satisfaction
Customer satisfaction is an excellent measure of quality management and analytics provides valuable insights into understanding customer needs, preferences and expectations. Businesses can even analyse customer feedback, reviews and sentiment data from various channels to gain a deeper understanding of customer perceptions and identify areas for improvement.
Quality management analytics allows you to make necessary adjustments to their processes. By continuously monitoring customer satisfaction metrics and acting on feedback in a timely manner, you can build stronger customer relationships and demonstrate a commitment towards quality.
7. Regulatory Compliance
In various industries, such as healthcare, pharmaceuticals and food manufacturing, compliance with quality standards and regulations is non-negotiable.
Analytics-driven quality management systems help ensure regulatory compliance by providing organisations with the tools and capabilities to monitor, analyse and report on key quality metrics. This way, organisations can conduct an ISO gap analysis to determine if their processes align with industry standards and regulations and demonstrate compliance.
In fact, analytics can also allow organisations to identify potential compliance risks, such as deviations from quality specifications or issues in documentation and take corrective actions to address them proactively.
Wrapping Up
As organisations continue to embrace digital transformation, analytics is undoubtedly a key aspect of effective quality management. It empowers businesses to unlock valuable insights, improve their processes, identify potential risks and make data-driven decisions to thrive in an increasingly competitive marketplace.