Ensuring a safe workplace is a priority for any organization, and the OHSAS 18001 standard offers a robust framework for achieving this. However, implementing an occupational health and safety management system based on the standard can be challenging.
From determining legislation requirements to securing top management support, implementing OHSAS 18001 requires careful planning and strategic solutions, especially if this is your first time working with an ISO standard.
This article will explore the biggest hurdles organizations might encounter when adopting OHSAS 18001 and how to address them.
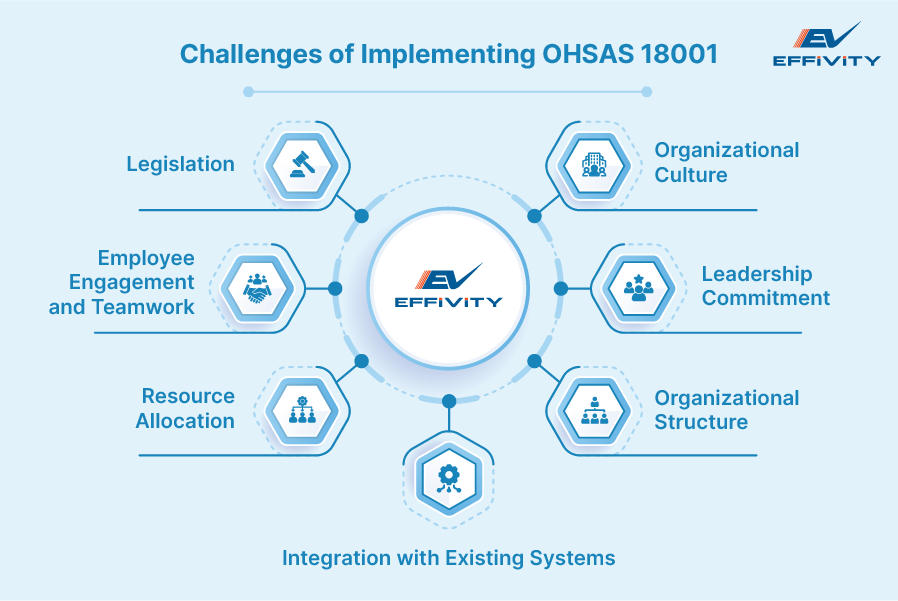
1. Legislation
Your occupational health and safety management system must meet the legal requirements of health and safety in your country or region. However, the regulatory landscape can be complex as it is constantly evolving, with different regions having varying regulations, posing significant challenges for organizations to keep up.
To manage this, it might be better to consult a specialist to understand which regulatory requirements apply to your business and make implementation easier. Further, it is important to stay informed about the latest regulations and regularly review and update OHSAS policies and procedures to reflect any changes in the legal environment.
2. Organizational Culture
If this is the first time your organization is implementing a health and safety management system, it can be easy to forget its importance. Employees might not see it as a priority, and processes might not be implemented to identify and address occupational risks.
As a result, it becomes necessary to create a culture that prioritizes health and safety rather than just implementing policies and procedures. It involves changing attitudes, behaviors, and the overall mindset of the workforce.
Section 4.2.2 of the standard discusses staff competence, training, and awareness to communicate the company's objectives and targets and enable good health and safety performance.
Leadership also plays a crucial role in driving cultural change. When management demonstrates a genuine commitment to health and safety, it sets a positive example for employees. Recognizing and rewarding safe behaviour and encouraging open communication can also foster a strong safety culture.
3. Employee Engagement and Teamwork
Employee resistance is another challenge that often hinders the OHSAS 18001 implementation process. Often, employees may even perceive the new system as an additional workload rather than a beneficial change.
So, apart from communicating the benefits, it can be helpful to engage employees in the planning and implementation process. In section 4.4.3.2 of OHSAS 18001, the standard suggests participation and consultation from expert team members.
When you consult and involve team members, it will build the knowledge of all parties concerned. Equally important, it will help you build relationships and trust between the team, making them feel valued and responsible for the system's success.
4. Leadership Commitment
Securing commitment from top management is another critical challenge. Without strong leadership support, the implementation process can face resistance and lack of direction.
Executive management's support is crucial to communicate the importance of health and safety management in an organization. Moreover, management's buy-in is crucial for allocating necessary resources and driving a safety culture.
Section 4.4.1 of the standard deals with the top management's roles, authority, responsibilities, resources, and accountability. It requires that the top management demonstrates its commitment to OHSMS and defines how to establish authority and responsibility within OHSMS.
5. Resource Allocation
Implementing OHSAS 18001 requires substantial resources, including time, money, and personnel. Smaller organizations, in particular, may find it challenging to allocate the necessary resources without affecting other critical operations.
The implementation and management process involves extensive documentation, training, audits, and continuous monitoring, all of which demand dedicated resources.
As a result, effective planning and budgeting are critical. Organizations should conduct a thorough assessment to determine the availability of required resources. It might also be a good idea to seek external expertise from consultants who can provide guidance and support, especially in the initial stages.
6. Organizational Structure
The structure of your organization, what it does, and how the processes are carried out will impact how the system is implemented. If your company operates from different global locations or has different types of operations, each of these will have different health and safety requirements.
This organizational complexity will add to the challenges of implementing the OHSAS as a "one-size-fits-all" approach, which might not work in addressing the OHSAS 18001 requirements.
7. Integration with Existing Systems
Many organizations already have various management systems in place, such as ISO 9001 for quality management or ISO 14001 for environmental management. Integrating OHSAS 18001 with these existing systems can be complex and may lead to confusion and overlap in processes.
This is where adopting an integrated management system can help unify multiple systems for seamless collaboration. An IMS allows organizations to streamline processes and reduce duplication by aligning all management systems under a unified framework. This approach can simplify compliance and improve overall efficiency.
Turn These Challenges to Your Advantage
Implementing OHSAS 18001 is a comprehensive process that involves overcoming several significant challenges. From employee engagement and resource allocation to determining the organization structure and ensuring leadership commitment, each obstacle requires careful planning and dedicated effort.
While the issues discussed are typical when establishing any OH&SMS, the risk of not addressing them effectively presents some opportunities. If you can help your company address these challenges proactively with proper planning and execution, your OH&SMS will be able to address the difficulties even before they arise.