Are you stuck in a process rut? Trying to juggle ISO 9001 compliance with actual efficiency can seem impossible. The pressure to meet compliance requirements while enhancing operational efficiency can lead to confusion and inefficiencies.
In this blog, we demystify the process approach with clear steps to identify your core processes, integrate ISO clauses, and optimize your performance. Equip your team to improve your overall productivity with quality management software.
What is the Process Approach?
A process, as defined by ISO 9001:2015, is any activity or set of activities that takes inputs and transforms them into outputs. This can apply to a variety of actions within an organization, like manufacturing parts, handling customer service calls, or developing marketing strategies.
Process vs Tasks
- Processes involve a transformation or a sequence of actions with a clear value addition from start to finish.
- Tasks like maintenance work or data entry might not necessarily result in transformation but are still essential.
Understanding this distinction will help you focus your Quality Management System on areas that truly impact your operational efficiency.
Identifying Core Processes
Identifying which processes are core to your QMS involves evaluating their impact on your company's objectives and compliance with ISO 9001 standards. Core processes are typically those that directly affect the quality of your products or services.
To identify core processes in your organization, consider the following:
- Does it directly impact customer satisfaction?
- Is it required for regulatory compliance?
- Does it have operational significance?
Some examples of core processes in a business are product development, fulfilling orders, customer service, and quality control.
Steps to Implement The Process Approach Effectively
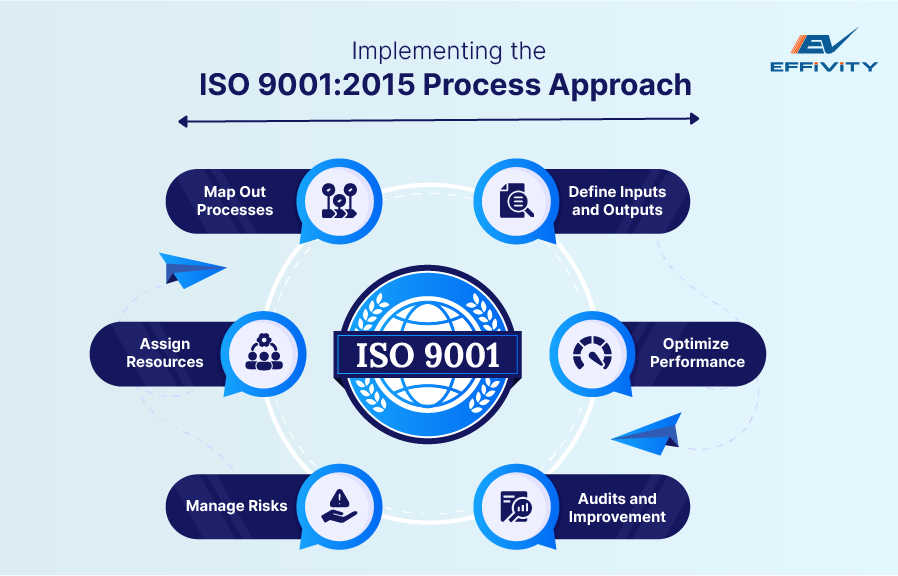
1. Mapping Out Processes
To effectively implement the ISO 9001:2015 process approach, visually map out the sequence and interactions of your processes. Create a process flowchart that outlines how each process flows into the next. Highlight interdependencies and how they collectively achieve the desired outcomes. Here's how you can approach this:
- Start by listing all critical processes that are fundamental to your business operations.
- Determine the logical order of these processes, from the initiation of a project or product lifecycle to its completion.
- Mark points where processes interact or overlap. This helps understand dependencies and potential bottlenecks.
2. Clarifying Inputs and Outputs
Each process in your QMS should have clearly defined inputs and outputs. This clarity helps optimize resource allocation and ensure quality outcomes.
- Define inputs: List all necessary resources, information, and materials required to start and maintain the process. For example, the manufacturing process may require raw materials, machine specifications, and operational guidelines.
- Specify outputs: Clearly articulate what each process is expected to yield. In customer service, the output might be resolved tickets and customer satisfaction ratings.
3. Assigning Resources and Responsibilities
Effective management of any process requires the right resources and clearly defined responsibilities. Determine what human, technological, and financial resources are necessary for each process. For the supplier management process, this might include inventory management systems, warehouse personnel, and logistics support.
Assign clear roles and responsibilities. Confirm that every team member knows their specific duties and how they contribute to the process.
4. Optimizing Process Performance
For continuous improvement and compliance with ISO standards, you must put in place key performance indicators (KPIs) for each process. These indicators should reflect both efficiency and effectiveness. Remember to:
- Choose KPIs that truly reflect the success factors of each process. For instance, in production, KPIs include production cycle time and defect rates.
- Implement a schedule for regularly tracking these KPIs to get real-time insights into process performance.
- Use QMS software solutions that can help you automatically track and report KPIs.
5. Addressing Risks and Opportunities
Proactively managing risks and identifying opportunities within processes is vital for sustaining business growth and resilience. Conduct regular risk assessments to pinpoint and resolve potential risks in each process. Encourage teams to continually look for process improvement opportunities.
6. Audit and Improve
The goal of any process-oriented QMS should be continual improvement, ensuring that processes stay relevant and efficient over time. Use insights from internal audits to pinpoint areas for improvement. Apply corrective actions based on performance reviews and audit results to refine processes. Strategies for continuous improvement include the Plan-Do-Check-Act cycle, which promotes ongoing evaluation and adjustment.
Integrating ISO Clauses with Processes
To improve the effectiveness of your Quality Management System, you must integrate ISO 9001 clauses with your organization's processes systematically. This integration ensures that each aspect of the standard is actively managed and continuously improved, aligning with specific operational activities.
Here's how you can link ISO 9001 clauses to specific processes:
- Start by understanding which clauses of ISO 9001:2015 are applicable to different aspects of your operations.
- Assign each clause to one or more processes that directly relate to the requirements of the clause. This helps in ensuring that all regulatory requirements are covered by your operational processes.
To make this simpler, you can create a clause-to-process linkage table like this:
Clause 4.4 (QMS and its Processes):
This clause requires the establishment, implementation, maintenance, and continual improvement of the quality management system. You should integrate this clause by ensuring that all processes are clearly defined, documented, and optimized to achieve the quality objectives and fulfill compliance requirements.
Clause 7.1.5 (Monitoring and Measuring Resources):
This clause demands that the organization determines and provides the resources required to guarantee valid and reliable monitoring and measuring of process outputs. Integrating this involves selecting appropriate tools, equipment, and techniques to monitor and measure the quality of products and services effectively and ensuring these tools are maintained and calibrated regularly.
Clause 9.2 (Internal Audit):
This clause requires the organization to conduct internal audits at pre-planned intervals to provide data on whether the quality management system meets the organization's requirements and the international standard. Integration means setting up a scheduled audit management program that evaluates all critical processes and using the findings to drive improvements in the QMS.
Clause 9.3 (Management Review):
According to this clause, top management must periodically review the quality management system's performance and suitability. Integrating this clause involves scheduling regular review meetings where management can assess and discuss reports from audits, customer feedback, process performance, and the status of improvement projects, making decisions as needed to improve overall effectiveness.
Develop Oversight Process
Developing comprehensive administrative and oversight processes is vital for covering all aspects of the ISO 9001 standard within your organization. These processes ensure that every operational activity is performed according to ISO guidelines and embed continuous improvement into your system.
To develop an oversight process, clearly outline the goals for each oversight process in terms of compliance, monitoring, and continuous improvement. Specify who will manage these processes and the resources they will require.
Final Thoughts
Embracing the ISO 9001:2015 standards may initially seem daunting, but with a structured approach to integrating these standards into your daily operations, you can boost both compliance and performance. Implementing a robust process approach allows you to define, monitor, and refine every aspect of your organization's activities. Leveraging quality management benefits ensures that your efforts are well-documented and insights from data are used for informed decision-making.