In 2024, maintaining top-notch quality standards has become more important than ever. Customer expectations and quality regulations constantly evolve, with the expectation that only the highest quality prevails. This means organizations have to ensure that they prioritize quality with efficient and reliable processes.
The IS0 9001 framework and QMS software help organizations achieve this. The continual improvement process is a key component of the ISO framework. Corrective action enables you to address and eliminate root causes of non-conformities. This resolves immediate issues and prevents future ones.
To successfully implement corrective actions, you must adopt a systematic approach. Let's examine all the steps you need to take to ensure that your business benefits from an efficient Corrective Action system.
What Are Corrective Actions?
Corrective actions are steps you take to eliminate the root cause of a problem in your processes. They go beyond simply fixing an issue temporarily.
For example, if a machine part breaks, replacing it is a temporary fix. However, if you investigate why it broke and take steps to ensure it doesn't happen again, that is a corrective action.
Corrections vs. Corrective Actions
Corrections are immediate responses to problems. They restore normal operations but do not address underlying issues.
Corrective actions, on the other hand, involve a deeper investigation to identify and eliminate the root cause of the problem. Corrective actions give you a more sustainable process improvement.
Root Cause Analysis
Root cause analysis is a systematic method to identify the fundamental source of a problem. It involves analyzing data, asking probing questions, and using specific methodologies to uncover the true source of an issue.
Effective root cause analysis helps with implementing corrective actions that lead to long-term solutions. This means you can enhance the overall efficiency and reliability of your processes.
Importance of Corrective Actions in ISO 9001 QMS
Implementing corrective actions has many benefits, including:
1. Address Root Causes:
Corrective actions help you tackle the underlying causes of problems, ensuring they do not recur.
2. Improve Efficiency:
Enhances your processes, leading to better product quality and customer satisfaction.
3. Reduce Long-Term Costs:
Prevents recurring issues, saving money in the long run.
4. Compliance:
Supports compliance with ISO 9001 standards, helping maintain certification and build trust with stakeholders.
Identifying When to Implement Corrective Actions
Not all situations in the workplace require corrective actions. Some criteria for implementing root cause analysis and corrective actions include:
-
Frequency and Impact:
Assess how often a problem occurs and its impact on operations. Frequent or significant disruptions require corrective actions.
-
Risk and Cost Assessment:
Consider the potential risks and costs of not addressing the root cause. Focus on significant, recurring issues to optimize resource allocation.
ISO 9001 Requirements
ISO 9001 does not require corrective actions for every minor issue but mandates a documented system for addressing significant non-conformities. You must establish procedures for identifying, analyzing, and resolving these issues. This creates a consistent approach to problem-solving and aligns with ISO 9001's emphasis on continual improvement processes.
Steps to Implement Corrective Actions
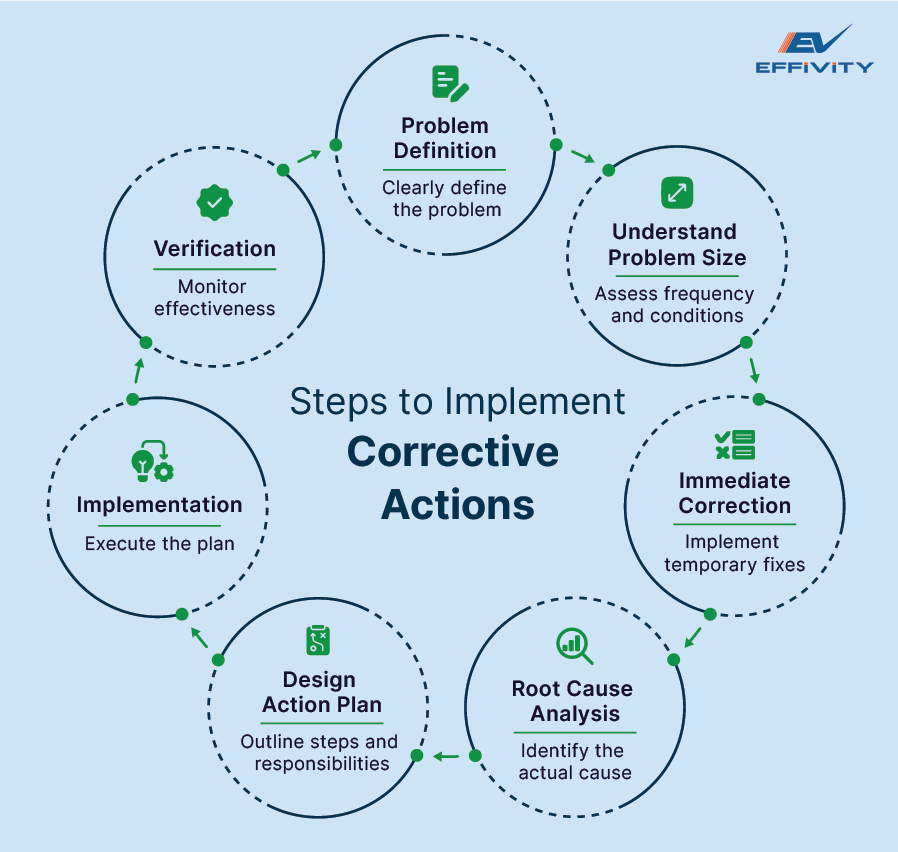
1. Problem Definition
First, clearly define the problem. Make sure it's a real issue and not just a perceived one. Use statements like "Should be" and "Is" to clarify the situation. For example, "The machine should operate without interruptions, but it stops frequently." This helps you frame the problem accurately.
2. Understanding the Problem Size
Next, assess the problem's size and frequency. Gather data on how often it occurs and under what conditions. Identify patterns, such as the problem happening only on specific days or during certain weather conditions. This information helps pinpoint the root cause and understand the problem's scope.
3. Immediate Correction
Implement an immediate correction to resume normal operations while you investigate further. This temporary fix allows production to continue and buys you time to find a permanent solution. At the same time, put measures in place to monitor the issue. This ensures you can track any recurrence during the investigation.
4. Root Cause Analysis
Conduct a thorough root cause analysis. Use techniques like the Five Whys, Fishbone Diagram, or Pareto Analysis. The goal is to dive deep and find the actual underlying cause of the problem. This step is critical because without understanding the root cause, you cannot implement an effective corrective action.
5. Designing a Corrective Action Plan
Develop a structure and comprehensive plan to address the root cause. Outline the steps needed to eliminate the problem, considering both feasibility and cost. Evaluate the return on investment to affirm that the corrective action is worthwhile. Include specific actions, responsible persons, and timelines in your plan.
6. Implementation
Execute your corrective action plan. Ensure everyone involved fully comprehends their responsibilities and the timeline. Communicate clearly and provide necessary resources to support the implementation.
7. Verification
After implementing the corrective action, monitor its effectiveness. Check if the problem recurs over a suitable period. This verification step is essential to confirm that the corrective action has resolved the issue. If the problem persists, revisit your root cause analysis and adjust your plan accordingly.
Tools and Techniques for Effective Corrective Actions
Root Cause Analysis Tools
Utilize various tools to identify the root cause of problems:
-
Five Whys:
This simple method involves asking "Why?" repeatedly until you uncover the fundamental cause.
-
Fishbone Diagram (Ishikawa):
This visual tool helps you categorize potential causes of problems, making it easier to analyze and identify the root cause.
-
Pareto Analysis:
Use this technique to prioritize issues based on their frequency and impact, helping you focus on the most significant problems.
-
Failure Modes and Effects Analysis (FMEA):
Examine possible failure points in a process and their effects, allowing you to address issues before they become significant problems.
Software Solutions
Leverage software solutions to streamline the Corrective Action process. QMS Software solutions provide structured workflows, automated tracking, and real-time monitoring. These features simplify the implementation and documentation of corrective actions, ensuring a consistent approach.
Best Practices for Corrective Actions
Tips for Successful Implementation
1. Documentation
Maintain thorough documentation of all steps taken during the Corrective Action process. This ensures consistency and provides valuable references for future issues.
2. Regular Training
Ensure staff are well-trained in identifying and addressing issues. Regular training equips them with the necessary skills and knowledge to carry out root cause analysis and implement corrective actions effectively.
3. Proactive Approach
Encourage a culture where employees actively look for potential problems and report them promptly. This proactive approach aids in quick identification and resolution of issues, preventing disruptions and improving overall efficiency.
Common Mistakes to Avoid
1. Incomplete Root Cause Analysis
Skipping steps or not digging deep enough can lead to ineffective solutions. Thorough analysis is crucial for identifying the true root cause of a problem.
2. Ignoring Verification Steps
Failing to monitor the effectiveness of implemented actions can result in recurring issues. Always verify that the corrective actions have resolved the problem and make adjustments if necessary.
Final Thoughts
Implementing corrective actions is essential for maintaining and improving your ISO 9001 QMS. By focusing on the root causes of problems, you ensure that issues are not only resolved but prevented from recurring. This proactive approach enhances process efficiency and reliability and contributes to better product quality and customer satisfaction.