ISO 9001 Certification is like the gold standard for quality-related benchmarks across all industries. If your organization is ISO certified, it means that you have demonstrated a consistent commitment to maintaining quality, increasing efficiency, and ensuring customer satisfaction. It shows all your stakeholders that you adhere to an internationally recognized standard and follow all best practices.
To get ISO 9001 certified, you need to follow several steps. It takes discipline to ensure that all your processes meet quality standards and that no issues are left unaddressed. While managing all the requirements of ISO can be time-consuming, it is certainly a rewarding process that brings many benefits to your organization.
Let's explore how to get ISO certification for small businesses and larger organizations. We will examine the steps you must follow and ways in which quality management software can help you achieve this milestone.
What is the ISO 9001 Certification?
The ISO 9001 for Quality Management Systems is a set of guidelines that dictate how your organization must handle quality-related tasks and improve efficiency and customer satisfaction. It covers various aspects of everyday operations to help you attain optimal performance. Being ISO-compliant is a qualifying requirement in many industries and markets. The ISO 9001 Certification shows that your organization is compliant.
ISO Certification is applicable across industries and for organizations of all sizes. It is also not product or service-specific. The standard's flexibility allows you to customize it to your organization's context.
How to Get ISO 9001 Certification?
To get ISO Certification, you must follow these three steps:
1. Plan
2. Implement
3. Get Certified
Now, let's look at each of these steps in detail.
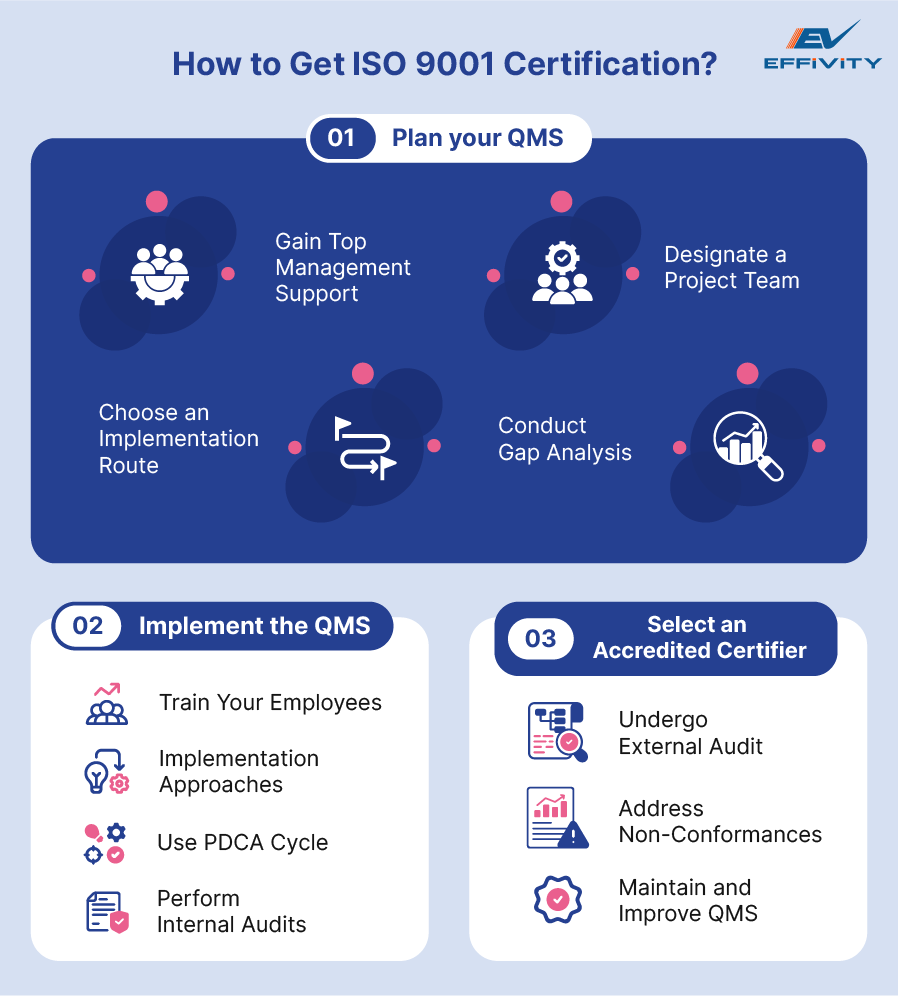
Step 1: Plan, Design, and Create Your Quality Management System (QMS)
1. Top Management Support
Start by getting support from top management, as their commitment is vital. They provide the resources needed to implement and maintain the system. ISO 9001:2015 necessitates top management to be responsible for specific actions within the system. Without their full support, implementation will likely fail.
2. Designate a Project Team
Form a dedicated project team to lead the implementation. This team should have a project manager and representatives from various departments. The project manager will oversee planning and coordination, and team members will bring expertise from their respective areas.
Assign well-defined roles and responsibilities to each employee Set specific goals and deadlines to keep the project on track. Regular meetings will help monitor progress and address issues promptly.
3. Choosing the Implementation Route
There are different ways to implement your QMS. Choosing the correct route depends on your resources and needs.
In-House Implementation
One option is to do everything in-house. You will need someone with knowledge and experience in ISO 9001. While this method may save money on direct costs, it usually takes longer to achieve certification.
Using Specialized Software
Another effective option is using specialized software. This software streamlines the process by incorporating the requirements of ISO 9001. It provides templates and modules that guide you through each step. Here's how it helps:
- Automates creation, storage, and management of documents
- Tracks changes and updates efficiently
- Provides step-by-step guidance
- The software includes pre-designed templates aligned with ISO 9001
- Offers dashboards and progress reports
- Identifies areas needing attention
4. Conducting a Gap Analysis
Before implementing QMS, a gap analysis must be performed. Compare your current system to the requirements of ISO 9001 and identify what's missing. This helps you create a project plan with clear steps and schedules.
Step 2: Implement the QMS
1. Train Your Employees
Ensure all relevant employees understand the Quality Management System (QMS) and their roles within it. Training should cover how to use the system, why it is being implemented, and the benefits it brings to the organization.
Conduct training sessions tailored to different departments. Make sure everyone knows how to access and use the QMS software.
2. Implementation Approaches
Choosing the right approach for implementing your QMS depends on your organization's needs and preferences. Here are two common approaches:
Fully Developed System
Some organizations prefer to develop the QMS fully before starting the implementation. This means creating all procedures, processes, and documents upfront. Once the system is complete, it is rolled out to the entire organization.
Phased Implementation
Others prefer a phased approach, where each section of the QMS is developed and implemented step-by-step. As each procedure or process is finalized, it is immediately put into practice.
3. Using the PDCA Cycle
The PDCA cycle stands for Plan, Do, Check, Act. It is a continuous loop that helps improve processes.
- Plan: Identify objectives and plan actions to achieve them.
- Do: Implement the planned actions.
- Check: Monitor and measure the results to see if objectives are met.
- Act: Take corrective actions based on the results and improve the process.
Use the PDCA cycle during implementation to ensure the QMS evolves and improves. Start by planning each phase, execute it, check the outcomes, and act on feedback. This method ensures continuous improvement and helps address any issues promptly.
4. Internal Audits
Internal audits are vital for ensuring your QMS functions as intended. They help verify that processes comply with ISO 9001 standards. Conduct regular internal audits to check compliance. This involves reviewing procedures, documents, and practices. Identify gaps and areas for improvement.
When audits reveal non-conformances, document them and take corrective actions. Develop a plan to address issues and prevent recurrence. This process helps maintain the integrity and effectiveness of your QMS.
Step 3: Get an Accredited Certifier
Choose an accredited certifier to audit your Quality Management System (QMS). Look for a certifier recognized by a national or international accreditation body. This ensures the certification process meets recognized standards and is credible.
1. The External Audit Process
The certifier will conduct a thorough audit of your QMS. This involves:
Document Review: The auditor examines your QMS documentation to ensure it meets ISO 9001 requirements.
On-Site Audit: The auditor visits your organization to assess the implementation of the QMS. They will observe processes, interview employees, and review records.
During the audit, the auditor may identify findings where your system does not fully comply with ISO 9001. These findings are categorized as:
- Non-Conformances: Major or minor deviations from ISO 9001 standards.
- Observations: Areas where improvements can be made.
2. Non-Conformance:
If the auditor identifies non-conformances, you will need to address them. Develop a corrective action plan to resolve these issues. Implement the necessary changes and provide evidence to the auditor. Once all findings are resolved to the auditor's satisfaction, the certifier will award the ISO 9001 certificate.
3. Post-Certification: Maintaining and Improving the QMS
ISO certificates are valid for three years. During this period, your organization must maintain and improve the QMS. The certifier will conduct periodic surveillance audits, usually annually, to ensure ongoing compliance. These audits are shorter and less comprehensive than the initial audit.
Final Thoughts
With careful planning and implementation, ISO 9001 certification is an achievable goal for every organization. After receiving ISO certification, it is important to stay committed to the principles of the standard to maintain the certification and ensure recertification.
While implementing ISO requirements manually can be challenging, with the help of quality management software you can automate most of the tasks and processes related to compliance management. With QMS software you can save time and resources, reduce errors and boost your overall efficiency.