For successful implementation of ISO 9001 within an organisation, the support and involvement of the top management cannot be understated. Leaders must stay on top of the regulatory requirements, allocate necessary resources and demonstrate commitment to quality management principles.
A key responsibility of the leaders within ISO 9001 implementation is management review. ISO 9001 clause 9.3.1 requires that the top management review the organisation's quality management system periodically to ensure it is suitable, adequate, effective and aligned with the company's strategic objectives.
The management review meeting is a formal meeting with the top management to identify any issues, improve processes, or address the need for change in various elements of the QMS.
Importance of Management Review
Surprisingly, management review meetings are not a requirement of ISO 9001 certification. Nonetheless, it is indispensable for running an effective QMS and meeting compliance requirements under the standard, as it allows management to be on top of the processes.
ISO management reviews are aimed at demonstrating continuous improvement by reviewing the standard guidelines and addressing areas of improvement so that the system stays aligned with the company's goals and objectives.
Here are the key objectives of conducting an ISO MRM-
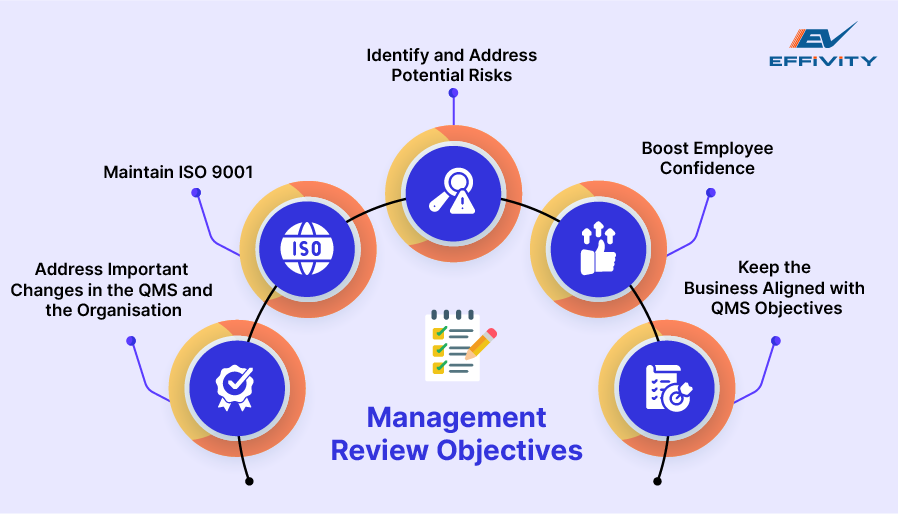
- To address important changes in the QMS and the organisation
- To maintain ISO 9001
- To identify and address potential risks
- To boost employee confidence
- To keep the business aligned with QMS objectives
To do a management review, a list of inputs is defined to determine if any changes are required in the Quality Policy and Objectives or the Quality Management system itself. In addition, the management also needs to evaluate potential areas for improvement in the organisation.
Which Management Review Inputs are Required?
The ISO 9001 management review requirements include seven inputs for the organisation that form the basis for conducting the review. However, it also gives the top management the flexibility to add more inputs to the review or use smaller reviews if they do not wish to conduct a meeting. Here are the seven ISO management review meeting inputs-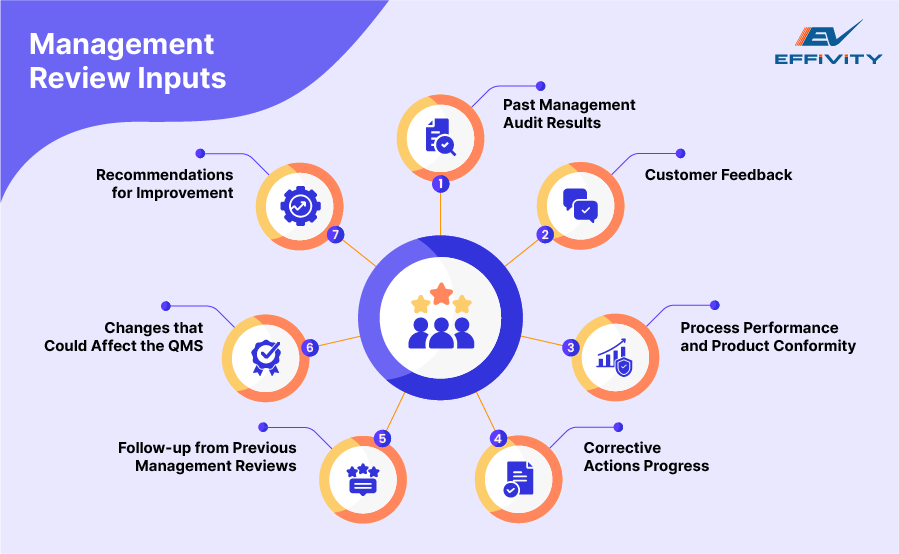
1. Past Management Audit Results
Audit reports are reviewed by the quality manager and the top management to determine results and include them in the internal audit planning for the year. Audit reports that carry the review information automatically become a key record of ISO management review.
2. Customer Feedback
Top management is interested in knowing how the business is dealing with customer feedback to ensure satisfaction. Maintaining records for customer feedback, actions required to address them and the person responsible will allow the top management to allocate resources and address any issues immediately.
3. Process Performance and Product Conformity
Your organisation must track KPIs to monitor processes, performance and non-conformity. Within management review, the top management must review these KPIs and make resource decisions based on them to ensure continuous improvement of processes.
4. Corrective Actions Progress
If a member of the top management participates in the corrective action review process, the management review is already in place. Moreover, management should also ensure that follow-up steps are defined to improve processes and that resources are allocated promptly to address them.
5. Follow-up from Previous Management Reviews
Another ISO 9001 management review requirement involves following up on the actions mentioned above to ensure they are implemented correctly. The records should also define and reflect the follow-up reviews.
6. Changes that Could Affect the QMS
Various outside influences, such as changes in the standard or legislation, can affect the QMS. As a part of the management review, it is important to track and record these changes to show that the review has been done.
In addition, any internal changes or their effects can be identified and reviewed by looking at internal audits, reviews of internal information and recommendations for improvement.
7. Recommendations for Improvement
Any recommendation for improvement, whether discussed by the top management or received through the employee suggestion system, should be logged and tracked so they can be reviewed easily. The top management must be involved throughout the organisation's review process to ensure the ISO management review's success.
Which Management Review Outputs are Required?
While the standard does not require you to maintain any minutes of meetings, it does require you to maintain records to demonstrate that the management review has identified outputs for QMS.
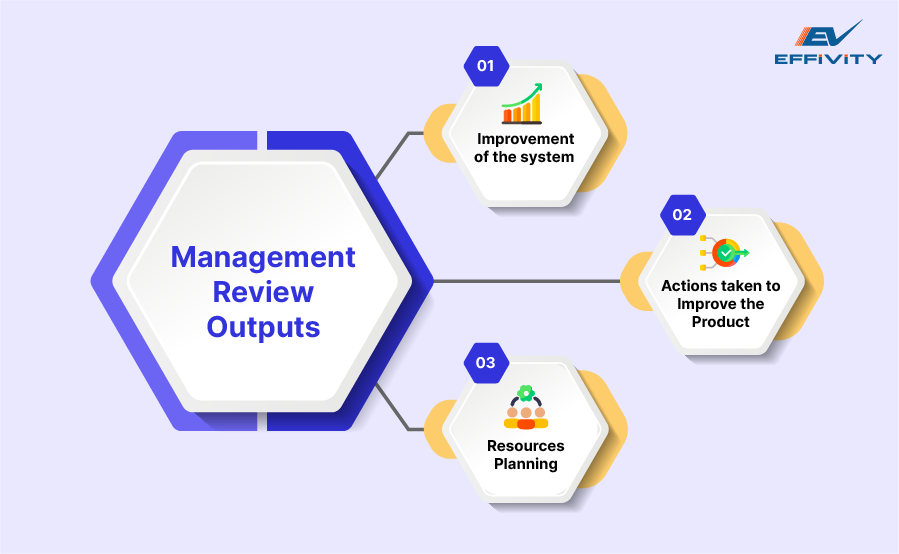
1. Improvement of the System
Management review outputs must include the action items to improve management systems. The involvement of the top management must be documented to demonstrate that QMS is improving. However, it must be ensured that these records are complete for them to be valid.
2. Actions Taken to Improve the Product
When the management reviews customer feedback and product conformity information, they must define and implement the action steps needed to improve the product and meet customer requirements. This will enhance product marketability and ensure that management review output is satisfied.
3. Resources Planning
One of the most important roles of top management is resource planning within the organisation to ensure accurate and effective allocation. Under management review output requirements, it is important to document the reasons behind their decisions.
Streamline Management Review with Effivity
Traditionally, organisations often conduct ISO management review meetings once a year or, at best, once a quarter. This is a long time to respond to customer complaints or resource requirements that may need immediate attention.
Instead, it is a better idea to involve the top management in all the management review processes. Doing it this way will also save time and money, which is always welcome in any organisation.
With Effivity, organisations can assign responsibility to top management to manage the input and output requirements under review. The software system will help ensure that the management is always up-to-date with the standard requirements and can conduct effective reviews.